Методика конструирования специальных станочных приспособлений. Исполнитель
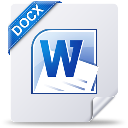
- Скачано: 51
- Размер: 178 Kb
Методика конструирования специальных станочных приспособлений.
План.
- Исходные данные и задачи конструирования.
- Типы специальных приспособлений.
- Последовательность конструирования.
- Обеспечение жесткости.
{spoiler=Подробнее}
Конструирование приспособления тесно связано с разработкой технологического процесса изготовления данной детали. В задачи технолога входят: выбор заготовки и технологических баз; установление маршрута обработки; уточнение содержания технологических операций с разработкой эскизов обработки, дающих представление об установке и закреплении заготовки; определение промежуточных размеров по всем операциям и допусков на них; установление режимов резания; определение штучного времени на операцию по элементам; выбор типа и модели станка. В задачи конструктора входят: конкретизация принятой технологом схемы установки; выбор конструкции и размеров установочных элементов приспособления; определение величины необходимой силы закрепления; уточнение схемы и размеров зажимного устройства; определение размеров направляющих деталей приспособления; общая компоновка приспособления с установлением допусков на изготовление деталей и сборку приспособления. Несмотря на четкое разделение функций, между технологом и конструктором должны существовать тесное взаимодействие и творческое содружество.
В качестве исходных данных конструктор должен иметь чертежи заготовки и детали с техническими требованиями их приемки; операционный чертеж на предшествующую и выполняемую операции; операционные карты технологического процесса обработки данной детали. Из них выявляют последовательность и содержание операции, принятое базирование, используемое оборудование и инструменты, режимы резания, а также запроектированную производительность с учетом времени на установку, закрепление и снятие обрабатываемой детали. Конструктору необходимы стандарты на детали и узлы станочных приспособлений, а также альбомы нормализованных конструкций. Полезно ознакомиться с аналогичными приспособлениями по литературным источникам и патентным материалам.
Из чертежей заготовки и готовой детали выявляют размеры, допуски, шероховатость поверхностей, а также марку и вид термической обработки материала. Из технологического процесса получают сведения о станке, на котором ведут обработку: его размерах, связанных с установкой приспособления (размеры стола, размеры и расположение Т-образных пазов, наименьшее расстояние от стола до шпинделя, размеры конуса шпинделя и т. д.), и общем состоянии. Необходимо также ознакомление со станком в цехе для выявления особенностей приспособления и наиболее выгодного расположения органов его управления.
Все эти сведения нужно иметь при конструировании каждого специального приспособления. При конструировании переналаживаемых и групповых приспособлений нужно, кроме того, определить детали, обрабатываемые с использованием данного приспособления и иметь по каждой детали перечисленные выше сведения.
Конструктору необходимо учитывать технологические возможности изготовления приспособления в условиях данного завода и программу выпуска изделий, чтобы выбрать наиболее рентабельную конструкцию и обосновать решение о применении в конструируемом приспособлении сменных быстроизнашивающихся деталей.
Полезно изучение опыта эксплуатации аналогичных приспособлений. Проработка исходных данных может привести к более рациональному построению технологических операций и иной схеме приспособления. Такие изменения после согласования с технологом вносят в карту технологического процесса.
Схема конструируемого станочного приспособления в основном определяется принятым построением данной операции обработки. По числу устанавливаемых для обработки заготовок схемы станочных операций делят на одно и многоместные, а по числу инструментов на одно и многоинструментные. В зависимости от порядка работы инструментов и расположения заготовок в приспособлении эти схемы могут быть последовательного, параллельного и параллельно-последовательного выполнения. При сочетании указанных признаков образуется несколько различных схем. Варианты схем оценивают по производительности и себестоимости с безусловным обеспечением заданного качества обработки.
Выбирая схему, стремятся к уменьшению штучного времени:
при поточном производстве это время должно быть равно темпу
выпуска изделий для обеспечения заданной производительности
линии. Уменьшение штучного времени достигается технологическими мероприятиями и мерами по совершенствованию конструкции приспособления. Повышая, например, жесткость приспособления, обеспечивают обработку с более производительными
режимами резания и совмещение различных переходов обработки
во времени. Вспомогательное время уменьшают, применяя быстро
действующие зажимные устройства и совмещая вспомогательное
время с основным путем использования поворотных приспособлений с отдельной позицией загрузки и снятия заготовки.
Приведенные признаки классификации станочных операций
могут быть использованы для построения схем приспособлений. Рассмотрим их характеристики применительно к задачам конструирования приспособлений на примере обработки отверстий
в корпусной детали (рис. 37, а).
Рис. 37. Типовые схемы компоновок станочных приспособлений
Признак 1 - по числу устанавливаемых заготовок: одно и многоместные приспособления (соответственно на рис. 37б, з, и). Признак влияет на компоновку и конструкцию приспособления.
Признак 2 – по числу используемых инструментов: (одно и многоинструментные приспособления рис. 37в, г). Вид, размеры и расположение инструментов влияют на конструкцию приспособления. При одновременном использовании нескольких инструментов требуется усиленное закрепление заготовки и расширение рабочей зоны для их размещения. По единовременному использованию нескольких инструментов приспособления можно разделить на одно и многосторонние (соответственно на рис. 37 г, е).
Признак 3 – по порядку применения инструментов и расположения заготовок: приспособления для последовательной (рис. 37 в), параллельной (рис. 37 г) и параллельно – последовательной (рис. 37 д) обработок. Этот признак может оказать влияние на компоновочные и конструкционные решения в части размещения установочных, зажимных и поворотных элементов приспособления.
Кроме приведенных, рассмотрим дополнительные признаки классификации станочных приспособлений.
Признак 4 – по числу позиций, занимаемых заготовкой по отношению к инструменту: одно и многопозиционные (рис. 37 г и в).
Признак 5 – по степени непрерывности обработки: приспособления для дискретной и для непрерывной обработки (рис. 37 в и ж).
Признак 6 – по участию человека в обслуживании приспособлений: ручные, полуавтоматические и автоматические.
Конструирование приспособления – творческий процесс. Для него характерны трудоемкость, много вариантность возможных решений и определенная последовательность (этапность) выполнения.
На первом этапе конструирования получают и анализируют исходные данные, определяют условия использования приспособления и предъявляемые к нему требования. Второй этап заключается в уточнении схемы установки. Зная принятую в технологическом процессе схему базирования заготовки, точность и шероховатость поверхностей базы, определяют тип и размер установочных элементов, их число н взаимное положение. Решение этого вопроса увязывается с требуемой точностью обработки на данной операции. На третьем этапе конструирования, зная величины сил резания, устанавливают место приложения сил закрепления и определяют их величину на основе расчетных данных. Исходя из регламентированного времени на закрепление и открепление заготовки, типа приспособления, конфигурации и точности заготовки, а также силы закрепления, выбирают тип зажимного устройства и определяют его основные размеры. На четвертом этапе устанавливают тип и размер деталей для направления и контроля положения режущего инструмента, на пятом выявляют необходимые вспомогательные устройства, выбирают их конструкции и размеры, исходя из массы заготовки, выполняемой операции и необходимой точности обработки. При выборе конструкции и размеров указанных элементов максимально используют имеющиеся стандарты.
Разработку общего вида приспособлений (шестой этап конструирования) начинают с нанесения на лист контуров заготовки.
В зависимости от сложности приспособления вычерчивают несколько проекций заготовки. Последнюю целесообразно показывать условными линиями (тонкими, штрих - пунктирными) для того, чтобы она выделялась на чертеже приспособления. Чтобы некасаться контура заготовки резинкой, заготовку часто вычерчивают с обратной стороны бумажной кальки в зеркальных проекциях. Вычерчивание приспособления производят затем с лицевой стороны.
Разработку общего вида ведут методом последовательного
нанесения отдельных элементов приспособления вокруг контуров
:заготовки. Сначала вычерчивают установочные детали, затем
зажимные устройства, детали для направления инструмента и
'вспомогательные устройства. После этого вычерчивают корпус
приспособления, который объединяет все перечисленные выше
элементы.
Из рассмотренного видно, что процесс конструирования приспособления - это процесс синтеза его элементов. Он состоит из выбора этих элементов, обеспечивающих заданные точность, производительность и экономичность; размещения элементов исходя из взаимосвязи между ними я выбора наиболее рационального соединения элементов оформлением корпуса приспособления. При конструировании и изготовлении приспособлений обеспечивают их высокую надежность по показателям безотказности, долговечности, ремонтопригодности, а в некоторых случаях и сохраняемости. Приспособления должны быть эргономичными, их обслуживание должно быть удобным и легким. Органы управления должны быть немногочисленными и располагаться в одном месте.
Общие виды приспособлений вычерчивают в масштабе 1:1 (исключение составляют приспособления для особо крупных или мелких деталей). На общем виде указывают габаритные размеры приспособления и размеры, которые нужно выдержать при его сборке и отладке, дается нумерация деталей и их спецификация с указанием использованных стандартов. На общем виде приспособления приводят технические условия на его сборку. В них указывают необходимую точность сборки приспособления требования к его регулировке и отладке, методы проверки при установке на станок, отделку л маркировку.
Далее производят деталировку. Рабочие чертежи выполняют только на специальные детали. Для сокращения маршрута составления чертежей общий вид и детали приспособления часто вычерчивают на эмульсированной кальке. С чертежа, выполненного на этой кальке карандашом, можно печатать достаточно четкие светокопии.
Для получения заданной точности обработки деталей (заготовок) конструируемое приспособление должно быть достаточно жестким. Жесткость в первую очередь обеспечивается в направлении действия сил закрепления и резания. Для повышения жесткости следует применять конструкции с малым количеством стыков, уменьшать, зазоры в соединениях и устранять внецентренное приложение нагрузки. Предпочтительны цельные или сварные конструкции деталей, менее желательны сборные конструкции.
Контактную жесткость стыков, работающих на сжатие, повышают, уменьшая шероховатость и волнистость сопряженных, поверхностей, применяя шлифование или шабрение. Возможность контактных деформаций в неподвижных стыках снижают сильной предварительной затяжкой соединяющих их крепежных деталей. Плоские стыки менее жестки на изгиб, чем на кручение. Равномерное расположение болтов благоприятно при работе круглого стыка на кручение. В стыках, работающих на изгиб, рекомендуется располагать болты неравномерно, смещая их но возможности дальше от нейтральной оси. В этом случае полезно уменьшать поверхность стыка сопрягаемых деталей в зоне нейтральной оси.
Жесткость стыков с шабреными и притертыми плоскостями
мало отличается от жесткости стыков с шлифованными плоскостями. Контактная жесткость закаленных деталей выше, чем у сырых. Достаточно высокую жесткость имеют стыки со строгаными плоскостями при совпадении рисок обработки. Контактная жесткость и демпфирующие свойства стыков повышаются при наличии тонкого клеевого слоя между сопряженными плоскостями.
Детали приспособлений должны быть жесткими при изгибе и
кручении. Корпус приспособления не должен деформироваться
при закреплении заготовок и деформировать стол станка, на котором он закреплен.
При вычерчивании общего вида и деталей приспособления назначают допуски на его размеры. По точности исполнения эти размеры можно разбить на три группы. К первой группе относятся размеры тех сопряжений, от которых зависит точность выполняемой обработки (например, расстояние между осями кондукторных втулок сверлильного приспособления; неточность этого размера непосредственно влияет на расстояние между осями просверленных в заготовке отверстий). К первой группе относятся также размеры установочных элементов, от точности которых зависит положение заготовки в приспособлении. Ко второй группе относятся размеры тех сопряжений, от которых точность обработки не зависит (например, размеры сопряжений зажимных устройств, выталкивателей и других вспомогательных механизмов). К третей группе относятся свободные размеры обработанных и необработанных поверхностей.
Вопросы для самоповторения.
- Что является исходным данным при конструирования приспособлений?
- Типы специальных приспособлений.
- Расскажите последовательность конструирования станочных приспособлений.
- Какими методами обеспечивается жесткость приспособлений?
{/spoilers}