Основные принципы проектирования технологических процессов механической обработки Исполнитель
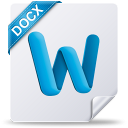
- Скачано: 58
- Размер: 22.78 Kb
Основные принципы проектирования технологических процессов механической обработки
План:
- Исходные данные для проектирования технологических процессов механической обработки.
- Установление планов и методов обработки.
- Выбор оборудования, приспособлений, режущего и измерительного инструмента.
- Установление режимов резания.
{spoiler=Подробнее}
Ключевые слова по теме лекции:
Рабочий чертёж; производственная программа; заготовка; материал; точность; припуск; вид производства; режим резания; режущий инструмент; приспособление; измерительный инструмент; операционная карта; маршрутная карта; эскизная карта.
1. Исходные данные для проектирования технологических процессов механической обработки
Основой для проектирования технологических процессов механической обработки являются подетальная производственная программа, составленная на основании общей производственной программ завода, рабочие чертежи машин и технические условия на выполнение.
Основные исходные данные для проектирования технологического процесса изготовления детали можно получить с рабочего чертежа детали.
На рабочих чертежах деталей указаны:
а) вид заготовки;
б) материал и его марка;
в) обрабатываемые поверхности;
г) обозначение класса шероховатости поверхности;
д) допуски и неточность обработки;
е) вид термической обработки.
Проектирование технологического процесса механической обработки деталей включает решение следующих основных вопросов:
1) установление вида производства и организационной формы выполнения технологического процесса;
2) определение величины партии деталей, запускаемых одновременно, для серийного производства и определение величины такта выпуска деталей для поточного производства;
3) выбор заготовок и определение их размеров;
4) установление плана и методов механической обработки;
- Выбор станочного оборудования, приспособлений, режущего и измерительноо нструментов;
- Определение размеров обрабатываемых деталей;
- Определение режимов работы;
- Определение нормы времени на обработку;
- Определение квалификации работы;
- Оценка технико-экономической эффективности спроектированного технологического процесса
2. Установление планов и методов обработки
При проектироании технологических процессов пользуются составленными на основании опытных данных таблицами средних величин экономической точности различных методов обработки.
При установлении последовательности операций следует руководствоваться следующими общими положениями:
1) в первую очередь надо обрабатывать поверхности детали, которые являются базами для дальнейшей обработки;
2) Затем следует обрабатывать поверхности, с которых снимается наиболее толстый слой металла;
3) Операции, где существует вероятность брака из-зи дефектов в материале или сложности механической обработки, должны выполняться в начале процесса.
4) Далее последовательность операций устанавливается в зависимости от требуемой точности поверхности: чем точнее должна быть поверхность, тем позднее она должна обрабатываться;
5) Поверхности, которые должны быть наиболее точнымии с наименьшей шероховатостью должны обрабатываться последними;
6) Совмещение черновой и чистовой обработки на одном и том же станке может привести к снижению точности обработанной поверхности вследствие влияния значительных сил резания и сил зажатия при черновой обработке и большего износа деталей станка.
3. Выбор оборудования, приспособлений, режущего
и измерительного инструмента
Устанавливая при проектировании технологического процесса план и метод обработки деталей, одновременно указывают, на каком станке будет выполняться операция, и приводят его характерстику: наименование станка, модель, основные размеры, мощность двигателя, стоимость и др.
Решающим фактором при выборе того или иного станка (если обработка возможна на различных станках, и обеспечивается удовлетворение технических требований к детали) является экономичность. В этом случае следует провести технико-экономическое сравнение обработки данной детали на разных станках при заданной годовой программе и принять ту модель станка, которая обеспечивает наименьшую трудоёмкость и наименьщую себестоимость обработки.
При проектировании технологического процесса обработки, наряду с выбором оборудования необходимо установить, какое приспособление необходимо для выполнеия на данном станке намеченной операции.
В единичном и мелкосерийном производстве широко применяется обработка без приспособлений или с приспособлениями универсального типа, которые являются принадлежностями станков (тиски, универсальные делительные головки и т.д.). В крупносерийном и массовом производстве применяют главным образом специальные приспособления, которые сокращают вспомагательное и основное время больше, чем универсальные, при более высокой точности.
Одновременно с выбором станка и приспособления для каждой операции выбирается необходимый режущий инструмент, обеспечивающий достижение наибольшей производительности, требуемой точности и класса шероховатости обработанной поверхности; указывается краткая характеристика инструмента, наименование и размер, марка материала и номер стандарта. Если для данной опреации требуется специальный инструмент, то в технологической документации отмечается - "специальный инструмент".
Применение того или другого типа инструмента зависит от следующих факторов: вида станка; метода обработки; материала обрабатываемой детали, её размера и конфигурации; требуемых точности и класса шероховатости обработки; вида производства.
При выборе и установлении метода обработки наряду с режущим инструментом указывается измерительный инструмент, необходимый для измерения детали в процессе её обработки или после неё с краткой его характеристикой: наименование, тип,, размер.При единичном и мелкосерийном производствеприменяется измерительный инструмент общего назначения - линейки, штангенциркули, микрометры, нутромеры, глубиномеры и т.д. В серийном и массовом производстве применяется специальный измерительный инструмент - калибры и шаблоны. Измерительный инструмент выбирается в зависиости от вида измеряемой поверхности и требуемой точности.
4. Установление режимов резания
Режим резания, устанавливаемый для обработки детали, является одним из главных факторов технологического процесса. Режим резания металла включает в себя следующие определяющие его основные элементы: глубина резания t в мм; подача s в мм/об; скорость резания v в м/мин; число оборотов шпинделя станка n в об/мин.
Исходными данными для выбора режима резания являются: вид заготовки; материал детали; механические свойства материала детали; величина припуска; требования по чистоте поверхности (шероховатость); форма, разверы и допуски на обработку.
Расчёт режимов резания проводится в следующем порядке:
- Выбирается глубина резания.
- Выбирается режущий инструмент.
- Определяется величина подачи.
- Выбирается период стоукости режущего инструмента.
- Определяется скорость резания.
- Определяется частота вращения шпинделя. Полученное значение частоты вращения корректируется по паспортным данным станка
- Определяется скорректированная скорость резания.
- Определяется сила резания
- Определяется мощность резания. Полученная мощность резания сопоставляется с мощностью электродвигателя станка. В том случае, если мощность резания больше мощности станка, необходимо уменьшить глубину резания или подачу произвести расчёт с пункта 5.
- Определяется основное время
При проектировании технологического процесса изготовления детали, составляют следующие карты на механическую обработку:
Маршрутная карта (ГОСТ 3.1404-71) содержит описание технологического процесса изготовления и контроля изделия по всем операциям различных видов работ в технологической последовательности с указанием данных по оборудованию, оснастке, материальным и трудовым нормативам.
Операционная карта (ГОСТ 3.1404-71) - содержит описание операции технологического процесса изготовлениия детали с указанием соответствующих данных по оборудованию, оснастке и режимам резания.
Карта эскизов (ГОСТ 3.1404-71) - содержит графическую иллюстрацию технологического процесса (операцию) изготовления детали.
Вопросы для самоконтроля
1. Перечислите исходные данные для проектирования технологического процесса механической обработки детали?
2. Какие данные можно узнать с рабочего чертежа детали?
3. Какими принципами нужно руководствоваться при проектировании технологических процессов механической оработки?
4. Как составляется план механической обработки?
5. Как производится выбор оборудования, приспособления, режущего и измерительного инструмента?
6. В какой последовательности производится расчёт режимов резания?
{/spoilers}