Введение конструкции деталей машин Исполнитель
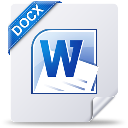
- Скачано: 18
- Размер: 246.5 Kb
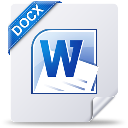
- Скачано: 18
- Размер: 123 Kb
Введение конструкции деталей машин
План:
1.Основные требования, предъявляемые к конструкции деталей машин
2.Основные категории работоспособности и расчета деталей машин.
3.Выбор материалов для изготовления деталей машин.
4.Замечания по вопросам расчета деталей машин.
5.Определение расчетных нагрузок.
6.Надежность машин.
{spoiler=Подробнее}
Опорные слова: работоспособность, расчеты, напряжения, износ,надежность, метеллы, пластмасса, нагрузка, конструция, ремонт.
Совершенство конструкции детали оценивают по ее надежности и экономичности. При этом под надежностью понимают вероятность безотказного выполнения определенных функций в течение заданного срока службы без внеплановых ремонтов. Экономичность определяется стоимостью материала, затратами на производство и эксплуатацию.
Основные критерии работоспособности и расчета деталей машин
Для того чтобы быть надежными, детали, прежде всего, должны быть работоспособными, т. е. находиться в таком состоянии, в котором они могут выполнять заданные функции в пределах технических требований (подробнее о надежности 9см).
Работоспособность деталей оценивают по прочности, износостойкости, жесткости, теплостойкости, вибрационной устойчивости. Значение того или иного критерия для данной детали определяют по условиям работы. Например, для крепежных винтов главным критерием является прочность, а для ходовых винтов — износостойкость.
При конструировании деталей их работоспособность обеспечивают главным образом выбором соответствующего материала и расчетом размеров изделия по основным критериям работоспособности.
Прочность является главным критерием работоспособности для большинства деталей. Непрочные детали не могут работать. Следует помнить, что поломки частей машины приводят не только к простоям, но и к несчастным случаям.
Различают статические и усталостные поломки деталей. Статические поломки происходят тогда, когда величина рабочих напряжений превышает предел статической прочности материала sв. Это связано обычно со случайными перегрузками, не учтенными при расчетах, или со скрытыми дефектами деталей (раковины, трещины и т. п.). Усталостные поломки вызываются длительным действием переменных напряжений, величина которых превышает характеристики усталостной прочности
материала (например,s-1).
Усталостная прочность деталей значительно понижается при наличии концентраторов напряжений, связанных с конструктивной формой детали (галтели, канавки, резьбы и т. п.) или с дефектами производства (царапины, трещины и пр.).
Основы расчетов на прочность изучают в курсе сопротивления материалов. В курсе деталей машин общие законы расчетов на прочность рассматривают в приложении к конкретным деталям и придают им форму инженерных расчетов. В инженерных расчетах большое внимание уделяют выбору расчетных схем и величин допускаемых напряжений (запасов прочности).
Неправильное назначение запаса прочности может привести к разрушению детали или к завышению веса конструкции и к перерасходу материала. В условиях больших масштабов производства машин перерасход материала приобретает весьма важное значение. Необоснованное увеличение веса таких машин, как транспортные, существенно понижает их эксплуатационные характеристики.
Факторы, влияющие на величину необходимого запаса прочности конкретной детали, весьма многочисленны и разнообразны: степень ответственности детали, однородность материала и надежность его испытаний, точность расчетных формул и определения расчетных нагрузок, влияние технологии изготовления детали, сборки узлов и т. д.
Если учесть, кроме того, все разнообразие условий работы современных машин и деталей, а также методов их производства, то станут очевидными большие трудности в раздельной количественной оценке влияния перечисленных факторов на величину запасов прочности. Поэтому в каждой отрасли машиностроения, основываясь на своем опыте, вырабатывают свои нормы запасов прочности для конкретных деталей. Эти нормы в приложении к расчету деталей общего назначения указаны в отдельных главах настоящего курса. Нормы запасов прочности не являются стабильными. Их периодически корректируют по мере накопления опыта и роста уровня техники. Наличие норм не умаляет существенного значения квалификации конструктора при выборе величин коэффициентов запаса прочности.
Кроме обычных видов разрушения (поломок) деталей, в практике наблюдаются случаи разрушения их поверхности. Последние связаны с контактными напряжениями.
Теорию контактных напряжений, как правило, не изучают в курсе «Сопротивление материалов». Эти напряжения являются предметом курса «Теория упругости». Расчеты многих деталей машин, изучаемые в данном курсе, выполняют по контактным напряжениям.
Поэтому ниже излагаются краткие сведения о контактных напряжениях и о разрушениях деталей, связанных с этими напряжениями. Кроме того, приводятся (без вывода) и объясняются те формулы, которые используются в дальнейшем как исходные для разработки методов расчета по контактным напряжениям.
Контактные напряжения возникают вместе соприкасания двух деталей в тех случаях, когда размеры площадки касания малы по сравнению с размерами деталей (сжатие двух шаров, шара и плоскости, Двух цилиндров и т. п.) *.
Если величина контактных напряжений больше допускаемой, то на поверхности деталей появляются вмятины, борозды, трещины или мелкие раковины. Подобные повреждения наблюдаются, например, у фрикционных, зубчатых, червячных и цепных передач, а также в подшипниках качения.
При расчете величины контактных напряжений различают два характерных случая:
а) первоначальный контакт в точке (два шара, шар и плоскость и т. п.);
Рис. 1.1
б) первоначальный контакт по линии(два цилиндра с параллельными осями, цилиндр и плоскость и т. п.).
На рис. 1.1 изображен пример сжатия двух цилиндров с параллельными осями. До приложения удельной нагрузки цилиндры соприкасались по линии. Под нагрузкой линейный контакт переходит в контакт по узкой площадке. При этом точки максимальных нормальных напряжений σн располагаются на продольной оси симметрии контактной площадки. Величину этих напряжений вычисляют по формуле
для тел из стали и других материалов с коэффициентом Пуассона μ=0.3
Здесь
где и — приведенные модуль упругости и радиус кривизны; Е1, Е2,R1,R2 — модули упругости и радиусы цилиндров.
Формула справедлива не только для круговых, но и для любых других цилиндров. Для последних R1 и R2 будут радиусами кривизны в точках контакта. При контакте цилиндра с плоскостью R2 = ОО. Знак минус в формуле (0.2) принимается в случае, когда поверхность одного из цилиндров вогнутая (внутренний контакт).
В зоне контакта материал подвергается трехосному сжатию *. При этом максимальные касательные напряжения действуют в точках, расположенных в плоскости уz на расстоянии 0,8а от поверхности контакта, где а — половина ширины площадки контакта,
Во многих случаях практики контакт деталей сопровождается скольжением, при котором поверхности контакта дополнительно нагружаются касательными силами трения.
Исследованиями установлено, что силы трения увеличивают максимальные касательные напряжения и приближают их к поверхности контакта. Так, например, при коэффициенте трения, равном около 0,2, получено
При вращении цилиндров под нагрузкой отдельные точки их поверхностей периодически нагружаются и разгружаются, а контактные напряжения в этих точках изменяются по прерывистому пульсационному циклу (рис. 0.2, г). Каждая точка нагружается только в период прохождения зоны контакта и свободна от напряжений в остальное время оборота цилиндра.
Переменные контактные напряжения вызывают усталость поверхностных слоев деталей. На поверхности образуются микротрещины с последующим выкрашиванием мелких частиц металла. Если детали работают в масле, оно проникает в микротрещины (рис. 0.2, а). Попадая в зону контакта (рис. 0.2, б*) трещина закрывается, а заполняющее ее масло подвергается высокому давлению. Это давление способствует развитию трещины до тех пор, пока не произойдет выкрашивание частицы металла (рис. 0.2, а). Выкрашивания не наблюдается, если величина контактных напряжений не превышает допускаемой.
Экспериментально установлено, что при качении со скольжением, например (см. рис. 0.2, а), цилиндры 1 и 2 обладают различной контактной выносливостью. Это объясняется следующим. Усталостные микротрещины при скольжении располагаются не радиально, а вытягиваются в направлении сил трения. При этом в зоне контакта масло выдавливается из трещин опережающего цилиндра 1 и запрессовывается в трещины отстающего цилиндра 2. Поэтому отстающий цилиндр обладает меньшей контактной выносливостью.
Кривые выносливости материала по контактным напряжениям подобны кривым выносливости по напряжениям изгиба, растяжения — сжатия и другим (см. курс сопротивление материалов и рис. 10.36). Здесь так же, как и при других напряжениях, имеется базовое число циклов Nно и соответствующий ему предел выносливости
Рис. 10.2
По определяются допускаемые напряжения при расчете на выносливость по контактным напряжениям.
Износ — процесс постепенного уменьшения размеров деталей, в результате трения. При этом может изменяться и форма деталей.
Износ деталей не должен превышать некоторой допустимой для данной машины величины. Детали, изношенные больше нормы, бракуют и заменяют при ремонте.
Интенсивность износа, а следовательно, и срок службы детали зависят от величины давления на поверхности соприкасания и скорости скольжения, а также от величины коэффициента трения и износостойкости материала.
Различают несколько видов изнашивания деталей: абразивный износ, износ при заедании, износ при коррозии и др. Основное значение имеет абразивный износ, происходящий вследствие царапающего действия неровностей поверхностей или твердых посторонних частиц (пыль, грязь и т. п.).
Для повышения износостойкости деталей широко используют смазку трущихся поверхностей, применяют антифрикционные материалы, специальные виды химико-термической обработки поверхностей и т. д.
При расчетах деталей, подверженных износу, уменьшают величину допускаемых давлений. В некоторых случаях это уменьшение весьма значительно. Так, например, на поверхности резьбы ходового винта токарного станка по условиям износа допускают удельные давления не более 8 -10 кгс/см2, в то время как в условиях простого нагружения без скольжения резьба может выдерживать значительно большие давления, например до 2000 кгс/см2.
Следует отметить, что износ выводит из строя большое число деталей машин. Он значительно увеличивает стоимость эксплуатации, вызывая необходимость проведения периодических ремонтов и замены деталей.
Износостойкость деталей машин существенно понижается при наличии коррозии, которая нарушает химическую однородность материала и увеличивает шероховатость поверхности детали. Коррозия является причиной преждевременного разрушения многих машин и конструкций.
Для защиты от коррозии применяют антикоррозионные покрытия или изготовляют детали из специальных коррозионно-устойчивых материалов. При этом особое внимание уделяется деталям, работающим в присутствии воды, пара, кислот, щелочей и т. д.
Жесткость наряду с прочностью является одним из основных критериев расчета. Во многих случаях именно по условиям жесткости определяют размеры деталей.
Расчет на жесткость предусматривает ограничение упругих деформаций деталей в пределах, допустимых для конкретных условий работы. Такими условиями могут быть, например:
а)условия работы сопряженных деталей (правильность зацепления двух зубчатых колес нарушается при больших прогибах валов;
изогнутый вал может заклиниться в подшипнике и т. д.);
б)технологические условия (точность и производительность обработки на металлорежущих станках в значительной степени определяются жесткостью .станка и детали и т. д.).
Нормы жесткости деталей устанавливают на основе практики эксплуатации и расчетов. Значение расчетов на жесткость возрастает в связи с широким внедрением высокопрочных материалов, у которых увеличиваются характеристики прочности (σв и σт), а модуль упругости. Е (характеристика жесткости) остается почти неизменным.
Теплостойкость — нагрев деталей машин может вызвать следующие вредные последствия:
1.понижение прочности материала и появление ползучести.
Ползучесть материала наблюдается главным образом в энергетических машинах с очень напряженным тепловым режимом (в газовых турбинах)*;
2.понижение защищающей способности масляных пленок, а следовательно, увеличение износа деталей;
3.изменение зазоров в сопряженных деталях (заклинивание,
задиры и пр.);
4.в некоторых случаях понижение точности работы машины.
В целях выявления влияния нагрева машины на ее работу производят тепловые расчеты и, если необходимо, вносят соответствующие конструктивные изменения (например, применяют охлаждение).
Виброустойчивость — вибрации вызывают дополнительные переменные напряжения и, как правило, приводят к усталостному разрушению деталей. В некоторых случаях вибрации снижают качество работы машин. Например, вибрации в металлорежущих станках снижают точность обработки и ухудшают качество поверхности обрабатываемых деталей. Особенно опасными являются резонансные колебания.
В связи с повышением скоростей движения машин опасность вибраций возрастает, поэтому расчеты на колебания приобретают все большее значение.
О выборе материалов для изготовления деталей машин
Выбор материала является ответственным этапом проектирования. Правильно выбранный материал в значительной мере определяет качество детали и машины в целом.
При изложении этого вопроса в курсе «Детали машин» предполагают, что изучающим известны основные сведения о свойствах машиностроительных материалов и способах их производства из курсов материаловедения, технологии материалов, сопротивления материалов.
Выбирая материал, учитывают в основном следующие факторы:
1)соответствие свойств материала главному критерию работоспособности (прочность, жесткость, износостойкость и др.);
2)весовые и габаритные требования к детали и машине в целом;
3)другие требования, связанные с назначением детали и условиями
ее эксплуатации (противокоррозионная стойкость, фрикционные свойства, электроизоляционные свойства и т.д.);
4)соответствие технологических свойств материала конструктивной форме и намечаемому способу обработки детали (штампуемость,свариваемость, литейные свойства, обрабатываемость на станках и т. д.);
5) стоимость и дефицитность материала.
Рекомендации по выбору материалов рассматриваются в отдельных главах курса в конкретном приложении к различным деталям.
Для изготовления деталей машин применяют различные материалы.
Черные металлы, подразделяемые на чугуны и стали, имею!' наибольшее распространение. Это объясняется прежде всего их высокой прочностью и жесткостью, а также сравнительно невысокой стоимостью.
Основными недостатками черных металлов являются большой удельный вес и слабая коррозионная стойкость.
Цветные металлы — медь, цинк, свинец, олово, алюминий и некоторые другие применяют главным образом в качестве составных частей сплавов (бронз, латуней, баббитов, дюралюминия и т. д.). Эти металлы значительно дороже черных и используются для выполнения особых требований: легкости, анти фрикционности, анти коррозионности и др.
Не металлические материалы — дерево, резина, асбест, металлокерамика и пластмассы — находят в машиностроении широкое применение.
Пластмассы являются новыми материалами, применение которых в машиностроении все более расширяется. Современное развитие химии высокомолекулярных соединений позволяет получить материалы, которые обладают ценными свойствами: легкостью, прочностью, тепло- и электроизоляцией, стойкостью против действия ' агрессивных сред, фрикционностью или анти фрикционностью и т.д.
Общим для всех пластмасс является способность формоваться вследствие пластических деформаций при сравнительно невысоких температурах и давлениях. Это позволяет получать из пластмасс изделия почти любой сложной формы высокопроизводительными методами: литьем под давлением, штамповкой, вытяжкой, выдуванием и т. д.
Вторым преимуществом пластмасс, которое следует подчеркнуть, является сочетание легкости и высокой прочности, характеризуемое отношением σв/ и называемое удельной прочностью. По этому показателю некоторые виды пластмасс могут успешно конкурировать с лучшими сортами стали и дюралюминия (табл.).
Таблица
Сравнение прочности металлов и пластмасс
Материал | Удельный вес у, Н/м310-4 | Предел прочности при растяженииМПа МПа | Удельная прочность |
Сталь лучших сортов | 7,8 | 1280 | 160 |
Чугун лучших сортов | 7,8 | 350 | 45 |
Дюралюминий | 2,8 | 390 | 140 |
Фенотекстослой | 1,4 | 150 | 110 |
Фенодревослой ... | 1 4 | 350 | 250 |
Стеклотекстослой | 1,8 | 540 | 300 |
Высокая удельная прочность позволяет широко использовать пластмассы в конструкциях, вес которых имеет особо важное значение (авиация, автомобилестроение и т. д.).
Основными потребителями пластмасс в настоящее время являются электрорадиотехническая и химическая промышленности. Здесь из пластмасс изготовляют корпуса, панели, колодки, изоляторы, баки, трубы и другие детали, подвергающиеся действию кислот, щелочей и т. п. В других отраслях машиностроения пластмассы применяют, главным образом, для производства сравнительно мало напряженных корпусных деталей, а также зубчатых колес, шкивов, вкладышей подшипников, фрикционных накладок, втулок, маховичков, рукояток и т. д.
Технико-экономическая эффективность применения пластмасс в машиностроении определяется в основном значительным снижением веса машин и повышением их эксплуатационных качеств, а также экономией цветных металлов и сталей. Замена металла пластмассами значительно снижает трудоемкость и себестоимость машиностроительной продукции. При замене черных металлов литьевыми пластмассами трудоемкость изготовления деталей уменьшается в среднем в 5—6 раз, а себестоимость — в 2—6 раз. При замене пластмассами цветных металлов себестоимость снижается в 4—10 раз.
Отрицательным, пока еще не устраненным, свойством пластмасс является склонность их к так называемому старению. Старение сопровождается постепенным изменением механических характеристик и даже размеров деталей в процессе эксплуатации. Этот недостаток все еще задерживает широкое распространение пластмасс в машиностроении.
В табл. 0.2 приведены механические характеристики наиболее распространенных материалов.
Замечания по вопросам расчета деталей машин
Большое значение в расчетах деталей машин имеют нормы, которым придают характер закона или рекомендации. Эти нормы следует рассматривать как обобщение большого опыта, гарантирующего работоспособность и рациональность конструкции.
Условия работы деталей машин часто бывают столь разнообразными и сложными, что их не всегда удается проанализировать и облечь в форму точного расчета. Поэтому в деталях машин широко применяют расчеты по приближенным формулам, а в некоторых случаях и по эмпирическим зависимостям.
Большое значение для приближенных расчетов имеет правильный выбор расчетной схемы, умение оценить главные и отбросить второстепенные факторы. Погрешности расчета по приближенным зависимостям компенсируют отмеченными выше нормами и рекомендациями. Так, например, неточность большинства расчетов на прочность принято компенсировать за счет допускаемых напряжений.
В курсе деталей машин встречаются две формы расчета — проектная и проверочная.
Проектный расчет — расчет, выполняемый при проектировании детали (машины) в целях определения ее размеров, материала и пр.
Проверочный расчет — расчет известной конструкции, выполняемый в целях проверки или определения норм нагрузки, срока службы и пр.
При проектном расчете число неизвестных обычно превышает число расчетных уравнений. Поэтому многими величинами задаются, принимая но внимание опыт и рекомендации.
В процессе проектирования расчет и конструирование органически связаны. При этом многие размеры, необходимые для расчета, конструктор берет из чертежа, а проектный расчет часто приобретает форму проверочного для намечаемой конструкции.
Об определении расчетных нагрузок
При расчетах деталей машин различают расчетную и номинальную нагрузку. Расчетную нагрузку, например крутящий момент Тр, определяют как произведение номинального момента Т на динамический коэффициент режима работы К: .
Номинальный момент соответствует паспортной (проектной) мощности машины и определяется по формуле
где N, кВт и n, об/мин — мощность и частота вращения двигателя; т) и 'и — коэффициент полезного действия и передаточное отношение кинематической цепи от двигателя до рассматриваемой детали.
Коэффициент К учитывает дополнительные динамические нагрузки, связанные в основном с неравномерностью движения, пуском и торможением. Величина этого коэффициента зависит от типа двигателя, привода и рабочей машины.
Если режим работы машины, ее упругие характеристики и массы известны, значение К можно определить расчетом. В других случаях величину К выбирают, ориентируясь на рекомендации справочников (см. табл. 0.3). Эти рекомендации составляют на основе экспериментальных исследований и опыта эксплуатации различных машин **.
О надежности машин
Надежности изделий всегда уделялось большое внимание. Значение надежности возросло по мере развития техники. В современный период быстрого технического прогресса проблема повышения надежности превратилась в одну из важнейших проблем. В курсе деталей машин излагаются основные понятия и конкретные меры повышения надежности деталей и узлов общего назначения.
Надежность — это вероятность безотказной работы в течение заданного срока службы в определенных условиях. Под заданным сроком службы понимается время до первого планового ремонта или между плановыми ремонтами.
Надежность можно определять для машины в целом или для отдельных ее агрегатов, узлов и деталей. Расчет надежности базируется на статистических данных. Статистические данные собирают путем наблюдений за изделием в эксплуатации или путем проведения специальных испытаний. Чем больше количество изделий, подвергавшихся испытаниям, тем точнее будет определена вероятность надежности.
Для оценки надежности могут быть выбраны различные показатели: число отказов в работе, средний срок службы в часах, число километров пробега и т. п. Целесообразность выбора того или иного показателя зависит от типа и назначения изделия. Если, например, из 1000 переключателей безотказно срабатывали 990, то надежность этих переключателей выражается коэффициентом R = 990/1000 =0,99.
Если для некоторых типов автомобилей установлен пробег 100 000 км до первого капитального ремонта, а среднестатистический пробег оказался равным 95 000 км, то коэффициент надежности этих автомобилей R =0,95.
Согласно теории вероятности коэффициент надежности сложного изделия выражают произведением коэффициентов надежности отдельных состовляющих элементов.
Формулу (0.6) используют для расчета надежности при проектировании машин. При этом величины Ri для отдельных деталей берут из каталогов (например, подшипники качения), определяют расчетом или специальными испытаниями.
Анализируя формулу (0.6), можно отметить следующее: 1. Надежность сложной системы всегда меньше надежности самого ненадежного элемента, поэтому важно не допускать в систему ни одного слабого элемента. Желательно, чтобы система состояла из равно надежных элементов.
2. Чем больше элементов имеет система , тем меньше ее надежность. Если, например, система включает 100 элементов с одинаковой надежностью Ri= 0,99, то надежность системы R = 0,99100 = 0,37. Такая система, конечно, не может быть признана работоспособной, так как она будет больше простаивать, чем работать.
Это позволяет понять, почему проблема надежности стала особенно актуальной в современный период развития техники по пути создания сложных автоматических систем. Известно, что многие такие системы (автоматические линии, ракеты, самолеты, математические машины и др.) включают десятки и сотни тысяч элементов. Если в этих системах не обеспечивается достаточная надежность, они становятся нецелесообразными. Например, раньше на изготовление некоторой детали массового производства был занят парк станков в количестве 100 единиц. При автоматизации производства этот парк станков был заменен одной автоматической линией. До автоматизации выход из строя одного станка снижал производительность цеха только на 1%. После автоматизации при повреждении автоматической линии производство детали полностью приостанавливается.
Для того чтобы автоматическая линия эффективно заменила прежний парк станков, она должна обладать более высокой надежностью, чем каждый станок в отдельности. Если учесть, что автоматическая линия несравненно сложнее станка, то будут понятны трудности выполнения этого условия.
Недостаточная надежность сложных систем приводит не только к снижению их производительности из-за большого количества ремонтных простоев, но и к большим ремонтным расходам. Во многих случаях затраты на ремонтное обслуживание сложных машин в несколько раз превышают стоимость их изготовления. Например, на ремонтное
График надежности имеет три характерные зоны. Первая зона от 0 до tn — период приработки. В начале этого периода интенсивность отказов имеет сравнительно высокие значения, затем снижается. Для периода приработки характерно проявление различного рода дефектов производства. По мере устранения этих дефектов интенсивность отказов понижается. Кроме того, вследствие приработочного износа все трущиеся детали автоматически доводятся до наиболее рациональных форм — устраняется местная концентрация
нагрузки, устанавливаются нормальные зазоры и т. п. Из этого следует, что для повышения надежности целесообразно производить обкатку изделия до сдачи его в эксплуатацию.
Вторая зона от tn до ti — период нормальной эксплуатации — характеризуется примерно постоянным значением интенсивности отказов. Причиной отказов здесь являются случайные перегрузки, а также скрытые дефекты производства, не проявившиеся в период приработки. К таким дефектам относятся, например, структурные дефекты материала, микротрещины и т. п.; вследствие этих дефектов снижаются усталостная прочность и износостойкость деталей. Очевидно, что устранить полностью все дефекты производства чрезвычайно трудно. Практически всегда остается некоторая вероятность появления этих дефектов. Величина такой вероятности зависит от культуры производства. Повышение надежности на участке нормальной эксплуатации зависит от многих факторов, которые рассмотрены ниже.
Третья зона t>tи — период проявления физического износа — характеризуется резким повышением интенсивности отказов. В этот период различные виды физического износа (абразивный износ, усталость материала и пр.) достигают таких значений, которые приводят к разрушению деталей или к нарушению нормальной работы машины. Машина требует очередного ремонта: В процессе ремонта заменяют или восстанавливают все поврежденные и ненадежные детали. После ремонта наступает новый период — приработки и нормальной эксплуатации. Из этого следует, что для повышения надежности машину целесообразно подвергать профилактическому ремонту до начала третьего периода.
Возвратимся к периоду нормальной эксплуатации. Приближенно постоянное значение интенсивности отказов в этой зоне позволяет получить сравнительно простую зависимость надежности от времени эксплуатации изделия:
где е — основание натурального логарифма.
Надежность R уменьшается с увеличением времени эксплуатации
по экспоненциальному закону (рис. 0.4). Интересно отметить, что
при t = 1/λ, всегда R = 1/е 0,37; при
t = 0,1/ R 0,9; при t = 0,01 /. R = 0,99 и т. д. Время эксплуатации при достаточно высокой надежности увеличивается с уменьшением ..
Рассмотрим далее основные пути повышения R- или уменьшения
Основы надежности закладываются конструктором при проектировании
изделия. Плохо продуманные, неотработанные конструкции, как правило, не бывают надежными. Конструктор должен отразить в чертежах, технических условиях и другой технической документации все факторы, обеспечивающие надежность изделия.
Вторым, не менее важным, этапом, обеспечивающим надежность, является производство конструкции. От качества производства конструкции зависит практическое выполнение всех средств повышения надежности, заложенных в ней. Величина интенсивности случайных отказов на участке нормальной эксплуатации определяется, главным образом, качеством производства.
Из предыдущего ясно, что разумный подход к получению высокой надежности состоит в проектировании по возможности простых изделий с малым числом деталей. Каждой детали должна быть обеспечена достаточно высокая надежность.
Рассмотрим дополнительно некоторые вопросы, имеющие общее значение в смысле надежности.
1.Надежность изделий тесно связана с их долговечностью. Изделия, долговечность которых меньше заданного срока службы, не
могут быть надежными.
2.Одним из простейших и эффективных мероприятий по повышению надежности является уменьшение напряженности деталей (повышение запасов прочности). Однако это требование надежности вступает в противоречие с требованиями уменьшения габаритов и веса изделий. Для примирения этих противоречивых требований рационально использовать высокопрочные материалы и упрочняющую технологию: легированные стали, термическую и химико-термическую обработку, наплавку твердых и антифрикционных сплавов на поверхность деталей, поверхностное упрочнение путем дробеструйной обработки или обработки роликами и т. п.* Так, например, путем термической обработки можно увеличить нагрузочную способность зубчатых передач в 2—4 раза. Хромирование шеек коленчатого вала автомобильных двигателей увеличивает срок службы по износу в 3—5 и более раз. Дробеструйный наклеп зубчатых колес, рессор, пружин и пр. повышает срок службы по усталости материала в 2—3 раза.
3.Эффективной мерой повышения надежности является также хорошая система смазки: правильный выбор сорта масла, рациональная система подвода смазки к трущимся поверхностям, защита трущихся поверхностей от абразивных частиц (пыли и грязи) путем размещения изделий в закрытых корпусах, установки эффективных уплотнений и т. п.
4.Статически определимые и самоустанавливающиеся системы
более надежны. В этих системах меньше проявляется вредное влияние
дефектов производства на распределение нагрузки.
5.Если условия эксплуатации таковы, что возможны случайные
перегрузки, в конструкции следует предусматривать предохрани-
тельные устройства (предохранительные муфты или реле максимального тока). Для уменьшения вредного влияния динамических нагрузок устанавливают упругие связи (упругие муфты).
6.В целях уменьшения отказов за счет дефектов производства все детали необходимо тщательно контролировать. Практика показывает, что специализация и автоматизация производства повышают качество и однородность изделий. Поэтому следует шире применять унифицированные детали массового производства. ГОСТы и нормали вырабатывают на основе глубоких исследований и большого опыта. Поэтому использованию стандартных элементов конструктор должен уделять большое внимание.
7.В некоторых изделиях, преимущественно в электронной аппаратуре, для повышения надежности применяют не последовательное, а параллельное соединение элементов и так называемое резервирование. При параллельном соединении элементов надежность системы значительно повышается, так как функцию отказавшего элемента принимает на себя ему параллельный или резервный элемент. Для параллельного соединения формула (0.6) несправедлива — см. [54].
В машиностроении параллельное соединение элементов и резервирование применяют редко, так как в большинстве случаев они приводят к значительному повышению веса, габаритов и стоимости изделий. Одним из примеров оправданного применения параллельного соединения могут служить двух- и четырехмоторные самолеты. Четырехмоторный самолет не терпит аварии при отказе одного и даже двух моторов.
8. Для многих машин большое значение, в смысле надежности, имеет так называемая ремонтопригодность. Отношение времени простоя в ремонте к рабочему времени является одним из показателей надежностное этой точки зрения конструкция должна обеспечивать легкую доступность к узлам и деталям для осмотра или замены. Сменные детали должны быть взаимозаменяемыми с запасными частями.
В конструкции желательно выделять ремонтные узлы. Замена поврежденного узла заранее подготовленным значительно сокращает ремонтный простой машины. При проектировании следует стремиться к равной долговечности всех деталей или к кратности их долговечности. Например, изделие имеет три группы деталей по долговечности:
I группа — срок службы 3000 ч
2-группа ‘’ – ‘’ ‘’ 6000 ч
3-группа ‘’ _’’ ‘’ 9000ч
Первый плановый ремонт предусматривает замену деталей I группы; при втором заменяют детали I и II групп; при третьем — I и III групп и т. д.
Перечисленные факторы, определяющие надежность, позволяют сказать, что надежность является основным показателем качества изделия. По надежности изделия можно судить как о качестве проектно-конструкторских работ, так и о качестве производства.
Вывод: изучив данную тему, студенты ознокомились с основными требованиями, предьявляемыми к кострукции деталей машин, их основные критерии работоспособности и расчета.
Контрольные вопросы:
1. По каким признакам оценивают совершенство конструкции детали?
2. Дайте определение понятию работоспособность?
3. Факторы, влияющие на величину необходимого запаса прочности конкретной детали?
4. Износ- это..?
5. Какие факторы учитываются при выборе материала для изготовления
детали?
6. Что такое надежность?
{/spoilers}