Комбинированный транспорт на карьерах Исполнитель
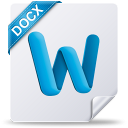
- Скачано: 36
- Размер: 585.98 Kb
Комбинированный транспорт на карьерах
План:
- Общие сведения
- Перегрузочные пункты при комбинированном транспорте
Цель занятия – формирование знаний об основных понятиях и принципах применение комбинированного транспорта на карьерах.
{spoiler=Продолжать Читать}
Общие сведения
Транспортную цепь в карьере между погрузочными и разгрузочными пунктами можно разделить на три звена: а) транспортирование по рабочим горизонтам и соединительным бермам; подъем (спуск) по вскрывающим выработкам на уровень господствующей поверхности; в) транспортирование на поверхности. Отдельные звенья могут отсутствовать.
Транспорт первого звена непосредственно обслуживает выемочно-погрузочные машины, поэтому должен обеспечить доступ к ним, высокую производительность экскаваторов, полноту выемки и требуемое качество полезного ископаемого, выполнение плановых объемов работ на уступах; он должен соответствовать геологическим и техническим условиям разработки, быть экономичным. Транспорт первого звена является сборочным, формирующим грузопоток.
Транспорт второго звена обычно обеспечивает преодоление значительной разности высотных отметок и требуемую пропускную способность коммуникаций. Особенности работы третьего транспортного звена зависят в основном от расстояния перевозок на поверхности до пункта разгрузки.
Комбинированный транспорт предполагает участие в одном грузопотоке от забоя до пункта конечной разгрузки (отвала, обогатительной фабрики, станции примыкания МПС) не менее двух видов карьерного транспорта (рис. 11.1). Каждый вид транспорта характеризуется своими техническими возможностями и экономическими показателями. Применение комбинированного транспорта позволяет снизить затраты на транспортирование горной массы, улучшить технико-экономические показатели смежных производственных процессов, перераспределить во времени объемы горных работ и т. д.
При этом необходима перегрузка горной массы из одних транспортных средств в другие, осуществляемая на перегрузочных пунктах. По месту расположения различаются перегрузочные пункты, устраиваемые на поверхности (рис. 11.1, а), борту карьера (рис. 11.1, б, в) и его дне (рис. 11.1, г). В последних двух случаях перегрузочные пункты являются полустационарными и периодически переносятся по мере понижения горных работ.
Чаще всего функции сборочного транспортного звена выполняет автотранспорт. Основные недостатки его – резкое (в 1,5-2 раза) уменьшение производительности при увеличении расстояния перевозок (рис. 11.2) с одновременным ростом затрат на транспортирование.
Рис. 11.1. Комбинации видов карьерного транспорта:
а, б-автомобильного и железнодорожного; в - автомобильного и конвейерного; г- автомобильного и канатного подъемника; д - автомобильного, гравитационного и железнодорожного; е- автомобильного, гравитационного и канатной подвесной дороги; ж- конвейерного и гидравлического; 1-автосъезды; 2-перегругзочные пункты; 3- железнодорожные съезды; 4- дробильная установка; 5- конвейеры; 6- перегрузочный (разгрузочный) бункер; 7-скиповой подъемник;8- рудоспуски; 9-штольня; 10-рудоскат; 11- канатная подвесная дорога; 12- роторный экскаватор; 13-гидромонитор; 14- водовод; 15– землесос;16- пульповод
Поэтому стремятся сократить длину откатки автосамосвалами до 0,7-1,5 км, а функции третьего или второго и третьего звеньев выполнять другими видами транспорта. Которые обеспечивают меньшие затраты на перевозки при больших расстояниях или позволяют резко сократить длину подъема (спуска) горной массы из карьера на господствующую поверхность.
Рис.11.2. Зависимость показателей работы транспорта от расстояния перевозок:
а- производительности автосамосвалов: 1- БелАЗ-540; 2- КрАЗ-222; 3- МАЗ-205; б- затрат на транспортирование: 1- автотранспортом; 2- железнодорожным транспортом
Уменьшение общих затрат на перевозки при расстоянии между перегрузочным и разгрузочными пунктами более 3-3,5 км может быть достигнуто комбинацией автомобильного и железнодорожного транспорта. Производительность второго при увеличении длины откатки от 5 до 10 км снижается лишь на 20-25%, затраты на перевозки при этом минимальны. Указанная комбинация используется также в случаях, когда железнодорожный транспорт невозможно применить по условиям вскрытия, интенсивности разработки. Усреднения и другим факторам. При комбинированном использовании этих видов транспорта резко улучшаются условия эксплуатации железнодорожного транспорта, который в этом случае работает в основном на постоянных путях с большей скоростью движения; резко сокращаются объем путевых и вспомогательных работ, их трудоемкость и расходы на них, упрощается схема путевого развития карьера, сокращается количество подвижного состава. Время погрузки составов и обмена поездов на перегрузочном пункте меньше, чем в забое, ввиду близкого расположения погрузочного и обменного пунктов. Стационарность путей, а следовательно и возможность их усиления позволяют применять мощный подвижной состав и существенно увеличить полезную массу поезда.
Сокращение длины подъема (спуска) горной массы из карьера достигается применением конвейеров или специальных видов транспорта: канатных подъемников, гравитационного, гидравлического транспорта, канатно-подвесных дорог и др., выполняющих функции только второго или второго и третьего звеньев (см. рис. 11.1).
Конвейерные подъемники, используемые в комбинации с автомобильным или железнодорожным транспортом для перемещения взорванных пород, отличаются от наклонных конвейеров, предназначенных для транспортирования таких пород, наличием перегрузочных пунктов.
Канатные подъемники имеют бесконечные или концевые тяговые канаты. Подъемники с концевыми канатами разделяются на скиповые, с вагонами тягачами, с автомобилями и троллейвозами, клетевые.
При использовании в качестве забойно-сборочного транспортного звена ленточных конвейеров возможна комбинация их с железнодорожным транспортом (при расстоянии перевозок по поверхности более 3-5 км) или с гидравлическим транспортом.
Перегрузочные пункты при комбинированном транспорте
При комбинации автомобильного и железнодорожного транспорта перегрузка горной массы производится непосредственно из автосамосвалов в думпкары (гондолы) на эстакадных перегрузочных пунктах, иногда через бункерные устройства, или с промежуточным складированием и использованием выемочно-погрузочных средств.
Эстакадные перегрузочные пункты (ЭПП) при односторонней разгрузке и фронтальном въезде автосамосвалов обычно представляют собой широкие перегрузочные площадки у откосов уступов или на полунасыпях, укрепленных подпорными стенками (рис. 11.3, а). При фланговом въезде и двухсторонней разгрузке автосамосвалов эстакады устраивают в виде насыпей с двумя подпорными стенками или выполняют из крупных железобетонных элементов (рис. 11.3, б). На перегрузочном пункте должен выдерживаться безопасный интервал между машинами (обычно не менее 20-25 м) и должно соблюдаться правосторонне движение.
Основные параметры ЭПП: высота, ширина и длина.
Высота эстокады между уровнями погрузочной и разгрузочной площадок =2,6÷2,9 м.
Ширина перегрузочной эстакады зависит от длины и ширины автосамосвала, радиуса его разворота =1,5, безопасного зазора между смежными автосамосвалами =0,5-1,5 м, числа сторон разгрузки, схем движения автомашин, числа и расположения въездов на ЭПП. При односторонней и последовательной двусторонней разгрузке =30÷50 м, а при одновременной двусторонней разгрузке в два состава =60÷100 м.
При односторонней разгрузке длина эстакад не превышает 120-150 м, а при двусторонней 60-70 м.
Производительность эстакадного перегрузочного пункта
, м3/ч, (11.1)
где - фактическая емкость кузова автосамосвала (в плотном теле), м3; - время обмена составов, мин (при тупиковом путевом развитии =10÷20 мин, при сквозном движении 35-40% меньше); - продолжительность разгрузки и маневров автосамосвалов на ЭПП, мин (=1,5÷2 мин); - число одновременно разгружающихся автосамосвалов
(11.2)
- число автосамосвалов, обслуживающих ЭПП; - коэффициент неравномерности движения (= 1,15÷1,25); - среднее время рейса автосамосвалов, мин.
Рис.11.3. Эстакадный перегрузочный пункт при односторонней разгрузкеифронтальном выезде (а) и при фланговом въезде и двусторонней разгрузке (б)
Достоинства эстакадной перегрузки: высокая производительность, небольшие капитальные затраты расходы, небольшое требующейся пространство, благоприятные условия для автоматизации. Основные недостатки: жесткая связь между автомобильным и железнодорожным транспортом, наличие дополнительных сооружений и сложность их переноса, увеличение износа подвижного состава.
Перегрузка горной массы с промежуточным складированием обычно осуществляется с помощью мехлопат. Могут применятся также одноковшовые погрузчики и специальные погрузочные машины. Различаются экскаваторные перегрузочные пункты (промежуточные склады): с устройством насыпи складируемой горной массы на горизонтальной площадке; с устройством премного бункера (прямика) экскаватора и движением автомобильного и железнодорожного транспорта на одном уровне; со складированием горной массы у откоса уступа.
Склады в виде насыпей (рис. 11.4, а) с одно- или двусторонней погрузкой создаются на широких рабочих площадках или на поверхности карьера. При односторонней погрузке и длине насыпи более 150-200 м устраивают ряд фронтальных въездов с уклоном не более 5% и шириной не менее 15-20 м со стороны нерабочего откоса; в других случаях въезды фланговые. Минимальная ширина верхней площадки насыпи при тупиковых маневрах автомашин 30-45 м, а при круговом или петлевом развороте 40-55 м.
Перегрузочные пункты (ПП) с прямиком (рис. 11.4, б) представляют собой траншею длиной 30-100 м, шириной до 30-40 м и глубиной до 3,5-4 м. Параметры прямика определяются радиусом вращения кузова, радиусом и высотой разгрузки экскаватора. С одной стороны прямика укладываю путь, а с трех других сторон устраивают подъездные площадки размерами не менее 4040 м.
Сооружение ПП со складированием горной массы под откос уступа (рис. 8. 4, в) заключается в крутой его заоткоске и тщательной подборке подошвы. Минимальная ширина разгрузочной площадки при сквозном проезде автосамосвалов составляет 35-40 м. Такие склады, сооружаемые при узких площадках на промежуточных горизонтах карьеров, имеют значительную протяженность (до 200-300 м).
Объемы, параметры и технология работы перегрузочных складов во многом зависят от их назначения. Рудные склады могут выполнять, кроме приемо-погрузочных, также регулировочные, резервные или раздаточные функции. Раздаточные функции заключаются в усреднение или раздельном складировании и отгрузке отдельных сортов полезного ископаемого.
Рис. 11.4. Типы экскаваторных перегрузочных пунктов
Технология валового складирования полезного ископаемого и вскрышных пород аналогично отвалообразованию при автотранспорте. Минимальная длина фронта разгрузки определяется по формуле (18.16).минимальная высота склада >2/3, где - высота расположения напорного вала рукояти (4-6 м для экскаватора ЭКГ-4,6 и ЭКГ-8И). , где - высота черпания экскаватора. Общая емкость склада
, м3, (11.3)
где - коэффициент неравномерности добычи (=1,05÷1,15); -объем поступающей на склад руды, м3/год; - число рабочих дней в году; - число дней, на которое рассчитывается запас руды на складе (обычно до двух недель).
Активная емкость склада , где =0,75÷0,8- коэффициент отгрузки складируемой руды. Чтобы не требовалась переукладка погрузочного пути на складе, его активная емкость не должна превышать объема одной заходки складского экскаватора:
(11.4)
Из формулы (8.3) определяется необходимая длина склада . Если требуемая протяженность склада невозможно по техническим условиям, необходима переукладка пути или переэкскавация руды из второй заходки.
Схемы путевого развития ПП предполагают устройство обменного пункта в виде разъезда с отцепкой или без отцепки локомотива (рис. 8.5, а, б) или обменного тупика (рис. 11.5, в). При двух экскаваторах на складе составы подаются по независимым путям или по одному пути пакетами (рис. 8.5, г, д). Минимальное время обмена достигается при схеме а:
, мин (11.5)
где: - длина поезда, м; - скорость движения локомотива, м/мин; - время отцепки локомотива от порожнего и прицепки к груженому составу, мин ().
Рис. 11.5. Схемы путевого развития экскаваторных перегрузочных пунктов.
1 – лебедка; 2 – направляющий блок.
На крупных карьерах при валовой перегрузке на складах работает до четырех-пяти экскаваторов ЭКГ-8И. среднечасовая производительность экскаватора на складе на 18-20% выше, чем в забое.
Достоинства экскаваторной перегрузки: большая производительность складов (до 30 млн.т/год), гибкость связи между автомобильными железнодорожным транспортом, простота и короткий срок сооружения, возможность усреднения руд. Недостатки: необходимость использования дополнительного мощного оборудования, увеличение затрат на перегрузку, значительные размеры складских площадок.
При комбинации автомобильного транспорта со скиповым подъемом перегрузка горной массы в карьере из автосамосвалов в скипы (рис.11.6, а) осуществляется непосредственно или через промежуточные бункера-дозаторы, емкость которых равна емкости скипов и автосамосвалов.
Рис. 11.6.Перегрузка горной массы из автосамосвалов в скипы и разгрузка скипов в бункер:
1 – скип; 2 – мост; 3 – предохранительный целик; 4 – рельсовый путь; 5 – наклонная эстакада; 6 – бункер; 7 – пластинчатые питатели.
При расположении ПП на промежуточном горизонте крутая траншея подъемника перекрывается сборным металлическим или железобетонным мостом для сквозного проезда автосамосвалов по транспортной берме. Автомашины разгружаются у края моста или на мосту, оборудованном поднимающимисялядами. Ширина моста должна обеспечить двухполосное движение автомашин, а ширина перегрузочной площадки – их свободный разворот (30-35м). Для одного подъемника необходимо иметь два перегрузочных моста: один в работе, а другой в монтаже или демонтаже.
Скипы разгружаются в железобетонные бункера, емкость которых не менее чем в 3-4 раза превышает емкость скипа и обычно составляет 200-300 м3 и более (рис. 11.6, б). При совмещении ПП с корпусом крупного дробления руда из скипов разгружается в дробилки, а далее транспортируется конвейерами.
При комбинации автомобильного и конвейерного транспорта в зависимости от типа перемещаемых пород полустационарные в стационарные перегрузочные пункты оборудуются пересыпными воронками, бункерами с питателями, грохотильными установками (рис. 8.7).
Пересыпные воронки, отличающиеся от бункеров меньшими размерами и отсутствием затворов, применяют при перегрузке мягких пород, доставляемых автосамосвалами грузоподъемностью до 5-7 т.
При перегрузке мелкоразрушенных полезных ископаемых (обычно угля) на поверхности и необходимости его аккумулирования сооружают заглубляемые в почву железобетонные бункера ячеечного или щелевого типа; из бункеров горная масса поступает на конвейеры, расположенные в горизонтальных подземных и далее наклонных галереях, выходящих на поверхность. Возможна также перегрузка мелкокусковатых пород на поверхности из средств колесного транспорта на конвейер с использованием полустационарных неглубоких бункеров траншейного типа, откуда, как и на абзетцерных отвалах, разгруженная горная масса экскавируется и перемещается на конвейер с помощью многоковшовых специализированных отвальных экскаваторов.
Рис. 11.7.Схемы перегрузочных пунктов:
а – грохотильного; б – грохотильно-дробильного; 1 – автосамосвалов; 2 – стационарный колосниковый грохот; 3 – бункер; 4 – дробилка; 5 – конвейеры.
Грохотильные установки применяют, когда выход негабаритных кусков (по условиям транспортирования конвейерами) не превышает 10-15%. При содержании негабарита до 1-3% (иногда 5%) возможно использование колосниковых грохотов, а при выходе негабарита более 3-5% - приводных грохотов, а при выходе негабарита более 3-5% - приводных грохотов (вибрационных, валковых, качающихся и др.). Полезная длина колосникового грохота должна быть не менее 6 м, угол их наклона должен быть в переделах 28-35°, щели должны иметь расширение к нижней части грохота. При размере транспортабельных фракций - 400 мм средняя ширина щели грохота 230-250 мм.
Перегрузочные пункты, помимо грохотильной установки, включают разгрузочную площадку или эстакаду с мостом для проезда автосамосвалов, бункера для подрешетного и надрешетного продуктов грохочения (последней может отсутствовать), а также питатели (обычно пластинчатые).
Дробильные установки перегрузочных пунктов оборудуются дробилками: щековыми, конусными или ударного действия. Щековые дробилки по сравнению с конусными конструктивно проще и меньше по размерам, но производительность их при одинаковый ширине разгрузочной, но производительность их при одинаковой ширине разгрузочной щели меньше (примерно в 3 раза), больше расход электроэнергии (почти 2 раза) и затраты на дробление. При использовании конусных дробилок кусковатость почти 15% дробленной руды превышает ширину разгрузочной щели в, а максимальный размер дробленных кусков ; степень измельчения конусными дробилками до 8, чаще 3-4.
Конусная дробилка ККД-1500/180 наиболее распространена на рудных карьерах. Щековые дробилки имеют приемные отверстия до 15002100 мм. Как правило, на перегрузочных пунктах устанавливают две щековые дробилки, заменяющие одну конусную.
Для дробления неабразивных горных пород (содержание кремнезема менее 10%) с пределом прочности на сжатие до 1500 кгс/см2 целесообразно применять дробилки ударного действия (молотковые и роторные). Масса их при одинаковой производительности со щековыми дробилками в 5 раз меньше. Степень измельчения составляет 6-8 (максимальная до 20). Удельный расход электроэнергии соответственно ниже на 80 и 20%, чем у щековых и конусных дробилок, и равен 0,5-1,5 кВт×ч/т.
Дробилка выбирается по размеру наибольшего куска загружаемого материала и по требуемой производительности при заданной ширине разгрузочной щели.
Установка грохотов на перегрузочном пункте перед щековыми дробилками экономически целесообразна, если в поступающей горной массе содержание транспортабельных конвейерами фракций составляет не менее 30-40% (вибрационный грохот) или 20% (колосниковый грохот).
Типом применяемой дробилки, размерами бункера, наличием или отсутствием грохота и питателей определяются параметры перегрузочных пунктов. Капитальные затраты зависят от строительного объема здания и применяемого оборудования.
При комбинации автомобильного и гравитационного транспорта непосредственная разгрузка автосамосвалов в рудоспуск (рудоскат) или в приемный бункер дробилки обычно осуществляется поочередно (один пункт разгрузки) или одновременно с двух-трех сторон приемного отверстия.
Перегрузка руды в вагонетки подвесной канатной дороги (ПКД) из узкоколейных вагонеток или автосамосвалов производится через промежуточный бункер. Вагонетки ПКД разгружаются также в бункер.
Ключевые термины:
транспорт первого звена транспорт второго звена
конвейерные подъемники транспорт третьего звена
канатные подъемники комбинированный транспорт
эстакадные перегрузочные пункты экскаваторная перегрузка
грохотильные установки дробильные установки
Контрольные вопросы
- На какие звенья разделяется транспортная цепь в карьере?
- Перегрузочные пункты при комбинированном транспорте.
- Типы экскаваторных перегрузочных пунктов.
- Достоинства экскаваторной перегрузки.
- Объясните схему перегрузочных пунктов.
Рекомендуемая литература по разделу:
- Анистратов Ю. И. Технология открытой добычи руд редких и радиоактивных металлов. – М., Недра, 1988.
- Горная энциклопедия в 5-ти томах. М., Советская энциклопедия, 1986.
- Мельников Н. В. Краткий справочник по открытым горным работам. М., «Недра», 1974. 424 с.
- Ржевский В. В. Открытые горные работы. Часть 1. – М., Недра, 1985.
- Ржевский В. В. Процессы открытых горных работ. М., «Недра», 1978. 542 с.
- Симкин Б. А. Технология и процессы открытых горных работ. М., «Недра», 1970. 215 с.
- Томаков П. И., Манкевич В. В. Открытая разработка угольных и рудных месторождений. М., Изд. МГГУ, 1995. 611 с.
- Технология открытой разработки месторождений полезных ископаемых, ч. I. Под общей ред. М. Г. Новожилова. М., «Недра», 1971. 635 с.
- Типовые элементы открытых разработок горнодобывающих предприятий черной металлургии. Л., изд. Гипроруды, 1971. 293 с.
- Теория и практика открытых разработок. Под общей ред. Н. В. Мельникова. М., «Недра», 1979. 512 с.
{/spoilers}