Методика исследования процессов трения и изнашивания. Исполнитель
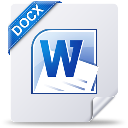
- Скачано: 55
- Размер: 415 Kb
Методика исследования процессов трения и изнашивания.
План.
- Методы измерения износа
- Методы измерения шероховатости поверхностей.
- Методы исследования поверхностей трения.
- Машины для испытания трения и износа.
{spoiler=Подробнее}
Измерение величины износа производят различными методами, в основе которых лежит требование минимальной затраты времени, возможности улавливания износа за короткий промежуток времени, минимального количества разборок и сборок сопряжений.
Рассмотрим некоторые из них.
Метод микрометража заключается в измерении микрометрами, индикаторами и другим мерительным инструментом линейного износа.
Преимущества этого метода: простота, доступность, возможность дифференцировать износ по разным точкам поверхности.
Недостатки метода: относительно большая погрешность приборов, которая, если величина износа невелика, может оказаться соизмеримой с величиной износа; необходимость разборки сопряжения для каждого измерения, что приводит к нарушению процесса изнашивания.
Методом взвешивания измеряют суммарный износ (суммарную потерю массы) по поверхности трения.
Преимущества этого метода: простота, доступность, относительно высокая точность.
Недостатки метода: невозможность дифференцирования износа по разным точкам поверхности; необходимость разборки сопряжения для каждого взвешивания; неприменимость данного метода к материалам, шаржируемым продуктами износа или посторонними частицами, а также к материалам, поглощающим влагу или масло.
Метод обнаружения продуктов износа в масле. Суть его заключается в том, что периодически отбирают пробы масла и по количеству находящихся в нем продуктов износа судят о степени износа. Количество продуктов износа в масле определяют химическим или спектральным анализом. '
Преимущества этого метода: возможность измерения износа без разборки сопряжения; высокая чувствительность.
Недостатки метода: невозможность определения износа каждой детали в отдельности (метод позволяет измерить суммарный износ всего сопряжения); сложность.
Методом радиоактивных индикаторов определяют износ детали по интенсивности радиоактивного излучения изотопов, удаляемых с поверхности трения вместе с продуктами износа. Материал изнашиваемых деталей предварительно активируется, т. е. в него вводится определенный радиоактивный изотоп одним из следующих методов:
а) введение радиоактивного изотопа в металл при плавке;
б) нанесение радиоактивного электролитического покрытия;
в) введение радиоактивного изотопа методом диффузии;
г) установка радиоактивных вставок;
д) облучение детали нейтронами.
По мере износа детали вместе с продуктами износа в масло попадает пропорциональное им количество атомов радиоактивного изотопа. По интенсивности излучения этого изотопа в пробах масла можно судить о величине износа.
Преимущества этого метода; возможность измерения износа без разборки сопряжения, непрерывного и периодического измерения износа, раздельного (дифференцированного) измерения износа деталей сопряжения.
Недостатки метода: сложность; необходимость специального оборудования, помещения, защитных и очистных устройств и т. д.
Методом встроенных датчиков определяют износ детали по изменению линейных размеров (или положения) этой детали, фиксируемому датчиком, встроенным о сопряжение. В качестве датчиков применяют различные датчики перемещений (индукционные, пневматические, тензометрические и др.), сигнал от которых записывают при помощи самописца, осциллографа и т. д.
Преимущества метода: относительно высокая точность; возможность измерения износа без разборки сопряжения, а также непрерывного или периодического измерения износа.
Недостатки: сложность метода, потребность в специальном оборудовании; затруднительное, а в отдельных случаях и невозможное раздельное измерение износа деталей сопряжения.
Метод искусственных баз. Этим методом величину износа определяет по изменению размеров суживающегося углубления (профиль которого известен), выполненного на изнашивающейся поверхности, Такими углублениями могут быть высверленное коническое отверстие, отпечатки в форме конуса или пирамиды, вырезанная лунка.
Рис. 9.1. Схема измерения износа методом вырезанных лунок.
Величину линейного износа при использовании отпечатка квадратной пирамиды на плоской поверхности вычисляют по формуле
9.1.
где Dh линейный износ в месте отпечатка;
h, h1 - глубина отпечатка до и после изнашивания;
d1 и d2 - длина диагонали отпечатка до и после изнашивания;
т - коэффициент пропорциональности (при угле пирамиды a=136° т= 7).
Величину износа плоской поверхности методом вырезанных лунок (рис. 9.1 ) определяют по формуле
(9.2)
где дополнительно l и l1 - длина лунки до и после изнашивания; r — радиус, описываемый вершиной резца.
Преимущества метода искусственных баз: высокая точность; возможность определения износа в разных точках.
Недостатки метода: местное вспучивание и искажение формы лунок; высокая трудоемкость; необходимость разборки узла; наличие специальных приборов для нанесения отпечатков и лунок и измерения их величины.
Методы измерения параметров шероховатости.
Параметры шероховатости поверхности определяют щуповыми и оптическими приборами. Для оценки шероховатости поверхностей по параметру Rz применяют двойной оптический микроскоп МИС-11. В нем микронеровности освещаются световой полосой, направляемой из осветительного тубуса под некоторым углом к поверхности. Линия пересечения световой полосы и микронеровностей наблюдается в увеличенном виде в визуальном тубусе. Микронеровности (для значений Rz от 80 до 2 мкм) измеряются окулярным микрометром или фотографируются с помощью фотонасадки. Сменными объективами достигается увеличение до 517 раз. Недостатком этого метода является высокая трудоемкость.
Наибольшее распространение получили методы определения параметров шероховатости при помощи щуповых профилометров и профилографов. Действие профилометра основано на принципе ощупывания исследуемой поверхности алмазной иглой с малым радиусом закругления и преобразования индуктивным методом ее колебаний в колебания напряжения. На шкале показывающего прибора профилометра оценка шероховатости дается по Rа.
Для записи микропрофиля поверхностей в виде профилограмм применяют профилографы, На рис. 9.2 представлена блок-схема
Рис. 9.2. Блок-схема щупового профилографа - профилометра.
щупового профилографа - профиломстра модели 201 завода «Калибр». Электрическая часть прибора включает в себя датчик, электронный блок 5 с показывающим прибором 6 и записывающий прибор 7. Магнитная система датчика состоит из сердечника 9 с двумя катушками 2. Катушка датчика и две половины первичной обмотки трансформатора 4 образуют балансовый мост, питающийся от генератора 3. При перемещении датчика по исследуемой поверхности алмазная игла 1, ощупывая неровности, поверхности, совершает колебания, приводя в колебательное движение относительно оси 8 якорь 10. Колебания якоря меняют воздушные зазоры между якорем и сердечником и тем самым изменяют напряжение на выходе трансформатора 4. Полученные изменения напряжения усиливаются электронным блоком, на выход которого подключается записывающий или показывающий приборы,
В качестве показывающего прибора используется отградуированный по параметру На микроамперметр постоянного тока. На записывающем приборе, представляющем собой магнитоэлектрический миллиамперметр постоянного тока, запись производится электротермическим способом на электротермической диаграммной бумаге. Общий вид профилографа- профилометра показан на рис. 9.3
Рис. 9.3. Общий вид профилографа - профилометра:
1 — стойка с кареткой; 2 —универсальный столик; 3 — датчик; 4 — мото-привод: 5 — электронный блок с показывающим прибором; 6 — записывающий прибор.
Техническая характеристика профилографа - профилометра
Пределы измерения Ra........... от 2,5 до 0,020.
Вертикальные увеличения......... 1000, 2000, 4000, 10000,
20000, 40000, 100000 и
200000.
Горизонтальные увеличения........ от 2 до 4000 (18 ступеней).
Измерительное усилие ощупывающей иглы не более 0,001 Н.
Радиус ощупывающей иглы........ 0,002 мм.
Наибольшая рабочая длина трассы ощупы-
вания при записи............. 40 мм.
Скорость трассирования профилографа . . . 0,2; 1,0 и 10 мм/мин.
Измерение волнистости поверхности производят на профило-графах, снабженных специальным приспособлением, а также специальными приборами для измерения волнистости.
МЕТОДЫ ИССЛЕДОВАНИЯ ПОВЕРХНОСТЕЙ ТРЕНИЯ
Для исследования состояния поверхностей трения и структуры поверхностных слоев в настоящее время применяют различные физические методы.
С помощью оптической металлографии исследования проводят на оптических микроскопах (увеличение 100—2000 крат) в светлом и темном поле с целью качественного определения фазового и структурного состава сплавов, а также количественного содержания фаз, размера, формы и распределения структурных составляющих. Применяют этот метод и для оценки состояния поверхностей трения (наличие повреждений, царапин, очагов коррозии, следов усталостного изнашивания и т. д.).
Измерение микротвердости. Этот метод в дополнение к оптической металлографии служит для идентификации различных фаз и структурных образований в сплаве, для определения степени упрочнения каждой фазы в исследуемой системе, степени упрочнения (или разупрочнения) отдельных участков поверхностей трения и прилегающих к поверхностям слоев материала.
Рентгеноструктурный анализ позволяет определять фазовый состав сплавов, исследовать тонкую структуру металла, степень совершенства кристаллической решетки, ориентировку кристаллитов, структурные изменения, протекающие в поверхностных слоях сплавов при термической и механической обработке и при трении. Электронная микроскопия, обладающая высокой разрешающей способностью, позволяет наблюдать изменение структур материалов на уровне, близком к атомарному, характер и даже протекание процессов разрушения поверхностного слоя, изучение структур границ зерен. Электронный микроскоп дает увеличение в 100000 раз и более.
Рентгеноспектральный микроанализ позволяет с разрешающей способностью, достигающей нескольких микрометров, исследовать распределение различных химических элементов в материале, что очень важно для решения многих металловедческих задач, а также для изучения и идентификации различных включений и выделений на поверхностях трения.
Метод непрыръшного рентгенографирования представляет собой разновидность метода рентгеноструктурного анализа и используется для исследования трущихся поверхностей. При проведении исследований оборудование можно приблизить к поверхности трения и фиксировать состояние металла в момент, непосредственно следующий за моментом выхода данной точки рабочей поверхности из контакта. С помощью этого метода фиксируется (фотометодом или ионизационным счетчиком) структура материала в состоянии, близком к тому, в каком он находился непосредственно в процессе трения и перед началом интенсивного охлаждения при выходе из контакта.
Метод масс-спектрометрии позволяет использовать газовыделение в качестве индикатора процессов, происходящих во фрикционном контакте.
МАШИНЫ ДЛЯ ИСПЫТАНИЯ МАТЕРИАЛОВ НА ТРЕНИЕ И ИЗНОС
Машины для испытания на трение и износ, довольно разнообразны по принципам действия и конструкции. Обычно они обеспечивают достаточно большой диапазон варьирования рабочих режимов, так как испытание на трение и износ требует учета большого количества факторов, влияющих па результаты. Фрикционные свойства зависят не только от материала испытываемой пары, но и от .конструкции узла трения. Обычно на практике применяют многоступенчатую схему испытаний, включающую четыре этапа (табл. 7.1). В зависимости от решаемой задачи отдельные этапы могут опускаться.
Таблица 9. 1
Этапы испытаний на трение и износ
Этапы | Вид испытаний | Цель испытаний |
1
2
3 4 |
Фнзико- механические лабораторные испытании материалов Испытание материалов на трение и износ на лабораторных установках Стендовые испытания узлов трения Натурные испытания |
Получение физика - механических характеристик материалов и прогнозирование по ним фрикционных свойств Оценка влияния физико-механических свойств и режимов трения на фрикционные свойства материалов Оценка влияния конструктивных особенностей узла трения Оценка взаимного влияния различных узлов механизма, надежности и долговечности работы механизма в целом |
Классификация машин для испытания материалов на трение и износ приведена на рис. 9.4. Конкретные модели машин снабжены устройствами, обеспечивающими возможность соответствующего вида испытаний (устройства для получения дополнительных, схем трения, создания дополнительных движений образца или контртела, создания ударов и вибраций, для температурных испытаний, для испытаний в различных средах, для измерения и регистрации силы трения, температуры, износа, для автоматизации процесса испытаний и т. д.).
Рассмотрим, какие машины применяются для испытания материалов на трение и износ.
Машина трения СМЦ-2 предназначена для изучения процессов трения и износа при трении качения с проскальзыванием, при трении качения без проскальзывания и при трении скольжения в условиях смазки или без нее. На рис. 9.5 дана принципиальная схема машины СМЦ-2 при испытании пары диск — диск.
Нижний испытуемый образец 10 приводится во вращение от электродвигателя 12 через клиноременную передачу 1 со сменными шкивами и шестерни Z0—Z1,. Верхний образец 9 приводится во вращение через шестерни Zо—Z2 и сменную пару Z3—Z4, с помощью которой устанавливается заданный коэффициент проскальзывания
где v1 и v2 — линейные скорости соответственно нижнего и верхнего образцов.
Верхний образец прижимается к нижнему путем поворота уравновешенной каретки 5 вокруг оси Z2-Z3 пружинным механизмом 6. Нагрузка отсчитывается по шкале 7, снабженной регулировочным устройством 8. Момент трения измеряется бесконтактным индуктивным моментомером 11, а частота вращения образца — электрическим счетчиком 3. При испытании пар трения диск — колодка и вал — втулка каретка 5 расцепляется с муфтой 4 и снимается с машины, а на ее место устанавливается соответствующее сменное приспособление. Для испытаний в смазке и в присутствии абразива машина снабжена съемными камерами. Защита машины от перегрузок осуществляется предохранительной
муфтой 2.
Момент трения может записываться на диаграммной ленте электронного потенциометра, размещенного вместе со счетчиком частоты оборотов в специальном настольном пульте. При работе по схеме диск по диску на машине могут проводиться также испытания образцов на контактную усталость, необходимые для моделирования работы зубчатых передач, колес и рельсов железнодорожного транспорта, подшипников качения и т. д. Техническая характеристика машины трения СМЦ-2
Виды испытываемых пар трения ........ диск—диск; диск —
колодка; вал—втулка.
Частота вращения ведущего образца, с-1...... 5; 8,33: 16,66.
Коэффициент проскальзывания, %.......... 0; 10; 35, 20; 100.
Наибольшая нагрузка на образцы, Н:
при замкнутой схеме (трение качения)..... 100 — 2000;
при незамкнутой схеме (трение скольжения) . . 200 — 5000.
Погрешность измерения нагрузки, %........ ±5.
Максимальный момент трения, Н-м 15.
Погрешность измерения момента трения, % ±5.
Тип моментомера ..................... электрический.
Испытание в средах ......................... смазка, абразив.
Машина МФТ-1 предназначена для определения фрикционной теплостойкости материалов, а также износа и коэффициентов трения различных материалов при коэффициенте взаимного перекрытия образцов, равном 1.
Рис. 9.6. Принципиальная схема машины МФТ-1
Кольцевой испытуемый образец 10 (рис. 7.6) установлен в самоустанавливающемся зажиме 11, закрепленном на шпинделе 12, который приводится во вращение от двигателя 15 постоянного тока с плавным регулированием скорости через двухступенчатую коробку скоростей 14 и клиноременную передачу 13. Переключением блока шестерни 16, 18 с помощью рукоятки 17 устанавливается нужный диапазон рабочих скоростей. Кольцевой контробразец 9 установлен в зажиме 8, соединенном с валом 20. Вал может поворачиваться в подшипниках 23 подвижного корпуса 22, который, в свою очередь, может без поворота по шариковым направляющим 21 вращением рукоятки 24 перемещаться относительно каретки 19. Образцы прижимаются пневматическим мембранным приводом 1, питающимся от сети сжатого воздуха или баллона, через шарик 2. Такая конструкция позволяет максимально устранить влияние осевой натрузки на измеряемый момент трения. Момент трения через рычаг 3 и регулируемый по высоте ползун 4 воспринимается тарированным упругим элементом 6 с индуктивным (преобразователем 5, жестко закрепленным в корпусе. Линейный суммарный износ образцов (сближение зажимов 8 и 11) измеряется индуктивным датчиком 7. Для измерения температуры предусмотрены термопары, которые впаиваются в образец 9. Корпус шпинделя и вал охлаждаются проточной водой. Машина МФТ-1 устанавливается на фундаменте и снабжается камерой, позволяющей вести испытания в жидких средах.
В процессе испытаний можно измерять и записывать на диаграмме момент трения, температуру и суммарный линейный износ образцов, а также измерять скорость вращения образца и суммарную наработку.
В машине предусмотрен также режим притирки образцов.
Техническая характеристика машины приведена ниже, Машина дисковая МДП-1 предназначена для определения коэффициентов трения и интенсивности изнашивания различных материалов при коэффициенте взаимного перекрытия, близком к нулю.
Истирающая поверхность 9 (металлический диск, сетка и т. п.) крепится к диску 10 (рис. 9.7), который приводится во вращение от электродвигателя 14 постоянного тока с плавным регулированием скорости через клиноременную передачу 13 и двухступенчатую коробку скоростей 16. Переключением муфты 11 рукояткой 15 устанавливают нужный диапазон рабочих- скоростей. При этом прямой передаче, минуя червячное зацепление 12, соответствует диапазон .минимальных моментов трения. Три пальчиковых образца 8 крепятся под углом 120°С друг к другу в цанговых захватах 7, которые с помощью винтовой 6 и конической 18 передач можно перемещать на различные радиусы трения. Диск 17 с захватами 7 установлен на шарикоподшипниках вала 20 в подвижном корпусе 21, перемещающемся поступательно относительно каретки 22 по шариковым направляющим 19. Вращением рукоятки 24 каретка приближается или удаляется от диска 10. В процессе испытаний образцы прижимаются пневматическим мембранным приводом 1 через упорный шарикоподшипник 23.
Возникающий момент трения с помощью рычага 3 и регулируемого устройства 2 воспринимается тарированным упругим элементом 4, жестко закрепленным на корпусе. Для измерения линейного износа служит индуктивный датчик 5, а для измерения температуры в зоне трения машина позволяет подключать шесть термопар. Пульт машины МДП-1 унифицирован, содержит ту же аппаратуру и обеспечивает те же возможности, что и на машине Л1ФТ-1.
Рис.9. Принципиальная схема машины МДП-1,
Технические характеристики машин трения
МФТ- 1 МДП- I
Количество одновременно испытываемых образцов..................1 3
Коэффициент взаимного перекрытия образцов . 1 0
Частота вращения подвижного контробразца, с-10,17 100 0,15...50
Диапазон регулирования частоты вращения 1 ... 600 1... 333
Усилие прижима образцов, Н......... 75 . . . 3000 100...4500
Погрешность измерения усилия, %.....±2,5 %.....±2,5
Пределы допустимый момент трения, Н-м 9 330
Погрешность измерения момента трения, % . ±5 ±5
Мощность привода, кВт........... 14 11,8
Радиус трения, мм.............. 24 60...150
Машина МПТ-1 предназначена для изучения процессов трения материалов при нормальных и повышенных температурах. Основным узлом машины является ползун 10 (рис. 7.8), на котором крепится нижний образец 9, имеющий форму пластины. Ползун совершает возвратно-поступательное движение, передаваемое от электродвигателя постоянного тока 17 через двухскоростной редуктор 18 и винтовую передачу 15 со скоростью 0,0001—0,01 м/с. Три верхних контробразца 8 крепятся в державке 5, жестко закрепленной в седле 6. Нагрузка на образцы в пределах 15—200 создается сменными грузами 7, устанавливаемыми на седло 6, Седло 6 с верхними образцами неподвижно относительно машины .я соединено двумя тягами 4 при помощи призм 2 со сменным упругим элементом 1 (в виде кольца), на котором наклеены тензодатчики. Сила трения, возникающая при движении ползуна, деформирует упругий элемент. Эта деформация через усилитель передается на показывающий прибор (миллиамперметр) или записывается осциллографом. Поступательная скорость ползуна, плавно изменяемая в пределах 1...100 при помощи регулируемого электропривода с магнитными усилителями ПМУ-1 и коробки скоростей, контролируется тахогенератором 16.
Рис. 9.8. Машина МПТ-1: а-принципиальная схема; б-размещение образцов.
Предусмотрено два режима работы машины: непрерывный я периодический. Величина возвратно-поступательного движения ползуна задается настройкой подвижных упоров 12 я 13 в пределах 30...100 мм. Перед началом испытаний приводится тарировка упругих элементов. Контробразцы 8 в державке притираются (для создания единой плоскости трения) на специальном приспособлении, которое поставляется в комплекте с машиной.
Машина комплектуется набором сменных упругих элементов, держателей образцов, а также сменными грузами, снабжена термокамерой 11 для испытания образцов при температуре до 200°С.
{/spoilers}