Обработка корпусов Исполнитель
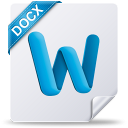
- Скачано: 43
- Размер: 172.01 Kb
Обработка корпусов
План:
1. Служебное назначение корпусов, технические требования, материалы и заготовки.
2.Этапы технологического процесса и их выполнение.
3.Особенности обработки корпусов на станках с ЧПУ.
4. Контроль корпусных деталей.
{spoiler=Подробнее}
Ключевые слова по теме лекции:
Корпусные детали; служебное назначение; поверхности детали; основные отверстия; соосность; параллельность; материал; этапы технологического процесса; обработка плоскостей; строгание; фрезерование; сверление; зенкерование; развёртывание; растачивание; фрезерование; резьбонарезание; оборудование; станки с ЧПУ.
1. Служебное назначение, требования и заготовки
Корпусные детали - базовые элементы механизмов, в них расположенных. К корпусным деталям относятся коробки скоростей станков, автомобилей, тракторов, блоки цилиндров двигателей, компрессоров, насосов, корпусы редукторов. От точности изготовления корпуса зависит точность работы всего механизма.
Технологически корпуса имеют следующие обрабатываемые поверхности:
1) плоскость основания (плоскость разъема) - имеет довольно жесткие допуски на параллельность, перпендикулярность (до 0,05-0,1мм) и с шероховатостью обработки до Rz20мкм,
2) вспомогательные плоскости - поверхности под крышки, фланцы, бобышки, и т.п. - шероховатость обработки до Rz40мкм, могут иметь ограничения по перпендикулярности к отверстию, закурываемому крышкой от (0,01 -0,2мм);
3) основные отверстия - под установку подшипников, крышек; обрабатываются по IT5 - 7 с шероховатостью Ra2,5 - 0,63 мкм; допуски на межосевые расстояния от 0,02 до 0.1мм; не параллельность или не перпендикулярность - 0,02 - 0,05мм;
4) вспомогательные отверстия: резьбовые (6Н - 8Н); под болты или шпильки (свободные размеры по IT14); под штифты (IT6 -8).
Выбор материала для изготовления того или иного корпуса зависит от действующих на него нагрузок. Как правило, для корпусов используется серый чугун, реже - алюминиевые сплавы и пластмассы. Высоконагруженные корпуса изготавливаются из стали.
В большинстве случаев заготовки корпусов получают литьем в землю с формованием по подмодельным плитам и использованием стержней. Корпусы из алюминиевых сплавов и термопластичных пластмасс могут получать литьем под давлением, а из термореактивных пластмасс - прессованием с последующим спеканием. Стальные корпуса получают литьем или сваркой из листовых элементов. Заготовки корпусов перед механической обработкой очищают от окалины и формовочной земли (пескоструйная обработка), зачастую окрашивают суриком.
2. Этапы технологического процесса механической обработки
корпусов и их выполнение
Обработка цельных корпусных деталей выполняется в следующей последовательности:
1) обработка основных технологических баз- плоскости основания и крепежных отверстий на них;
2) обработка всех остальных вспомогательных плоскостей;
3) черновая и получистовая обработка основных отверстий;
4) обработка всех оставшихся вспомогательных отверстий;
5) отделочная обработка основных отверстий.
При обработке корпусов деталей, имеющих плоскость разъема, типовой технологический процесс следующий:
1) обработка плоскости разъема корпуса;
2) обработка базовых плоскостей;
3) сверление и нарезание резьбы, обработка отверстий под штифты по плоскости разъема корпуса;
4) сборка частей корпуса с фиксацией штифтами;
5) совместная обработка остальных плоскостей и оснговных отверстий.
В условиях единичного и мелкосерийного производства механическая обработка корпусных деталей начинается с разметки, когда с помощью рейсмуса наносят риски центров основных отверстий и контуры детали. Центры отверстий кернятся, а углубления от керна служат для выставки заготовки на станке при наличии жесткого центра в шпинделе. Затем центр заменяется режущим инструментом и проводится обработка.
В средне - и крупносерийном производстве базирование деталей на станках проводится с помощью специальных приспособлений, а на автоматических линиях могут использоваться приспособления - спутники.
Обработку наружных плоскостей корпусов проводят строганием, фрезерованием, точением, обдирочным шлифованием и протягиванием. Строгание широко используется в единичном и мелкосерийном производстве из-за простоты наладки и инструмента. Для малогабаритных корпусов применяется поперечное строгание, для крупногабаритных - продольное (рис. 2.1).
Рис.2.1. Схемы строгания плоскости:
а) продольное строгание; б) поперечное.
Производительность строгания низкая. Повысить ее можно путем одновременной обработки группы деталей, расположенных последовательно на столе станка, либо обрабатывая несколько поверхностей одного корпуса с использованием суппортов продольного - строгального станка.
Торцевое фрезерование - наиболее распространенный вид обработки плоскостей в серийных видах производства. Для повышения производительности фрезерования можно использовать продольно-фрезерные многошпиндельные станки, устанавливая заготовки корпусов в ряд (рис.2.2,а), обрабатывая у них сразу несколько поверхностей одновременно (рис.2.2,б), либо используя обработку заготовок с перекладкой (рис.2.2,в).
Рис. 2.2. Повышение производительности обработки на продольно-фрезерном станке: а) многоместная обработка; б) одновременная обработка верхних и боковых плоскосей; в) обработка с перекладкой.
Производительность фрезерования повышается также при использовании карусельно- и барабанно-фрезерных станков (рис.2.3).
Рис.2.3. Непрерывное фрезерование поверхностей:
а) на карусельно-фрезерном станке с одним шпинделем; б) на карусельно-фрезерном станке с двумя шпинделями (черновая и чистовая обработка); в) на барабанно-фрезерном станке; 1- фрезы; 2 - обрабатываемые детали; 3 - стол станка; 4 - барабон.
Время обработки на вертикально-фрезерном станке можно уменьшить установкой двух приспособлений и маятниковым фрезерованием.
В массовом производстве плоскости корпусов часто обрабатывают на специальных протяжных станках (рис.2.4).
Рис.2.4. Схемы станков для непрерывного протягивания плоскостей: а) с карусельным столом; б) с барабаном; 1- обрабатываемые детали; 2- протяжка.
Корпуса - фланцы, имеющие наружные и внутренние поверхности вращения, обрабатываются на токарно-карусельных станках точением.
Окончательная обработка плоскостей корпусных деталей, а иногда и их обдирка в серийных видах производства проводится на плоскошлифовальных станках торцом сегментного сборного круга, чашечным кругом или переферией плоского дискового круга (рис.2.5).
Рис.2.5. Схемы наладок шлифования плоскостей: а) торцом сегментного круга; б) переферией круга.
После фрезерования плоскости основания (разъема) сверлятся на ней отверстия под крепеж, два из которых обязательно подвергаются развертыванию (технологически) под установку корпуса для дальнейшей обработки на плоскость основания и два пальца - цилиндрический и срезанный. Обработку проводят на радиально-сверлильном станке по кондуктору, на вертикально-сверлильном станке со специальной многошпиндельной головкой (крупносерийное производство) или агрегатно-сверлильном станке. В двух последних случаях для обработки отверстий под пальцы могут использоваться комбинированные инструменты сверло-развертка.
Основные отверстия в корпусах начерно и получисто обрабатываются на расточных, токарных, токарно-карусельных, радиально и вертикально-сверлильных, а так же на агрегатных станках. При этом отверстия малого диаметра (до 40 -50мм) обрабатываются «мерным» инструментом - сверла, зенкеры, развертки - а отверстия больших диаметров - расточными оправками, резцовыми головками, борштангами и т.д. Для повышения точности обработки как в первом, так и во втором случаях используют приспособления с дополнительным направлением (опорой) режущего инструмента (рис. 2.6.). Точность взаимного расположения отверстий достигается разметкой, пробными расточками (индивидуальное и мелкосерийное производство), растачиванием в приспособлениях (серийное и массовое производство), координатным методом (на расточных станках и станках с ЧПУ).
Рис.2.6. Методы направления инструмента при обработке отверстий в корпусных деталях: а) -переднее направление; б) - заднее направление; в) - переднее и заднее направление.
Для высокоточных работ (изготовление оснастки) используются координатно-расточные станки с точностью установки координат до 1мкм.
В крупносерийном и массовом производствах растачивание корпусных деталей проводится обычно на агрегатно-расточных станках с возможностью осуществлять на них также сверление, зенкерование, развертывание, нарезание резьбы и т.д. с нескольких сторон корпуса за одну или несколько позиций. При необходимости выдержать соосность отверстий в нескольких стенках корпусной детали обработку ведут одновременно напроход (рис.2.7.)
Рис.2.7. Растачивание отверстий под подшипники распределительного и коленчатого валов в блоке цилиндров двигателя.
Отделочными видами обработки основных отверстий являются тонкое растачивание, внутреннее шлифование, хонингование, раскатка роликами.
Тонкое (алмазное) растачивание применяют для получения заданной точности размеров основных отверстий чугунных корпусных деталей. Этот вид обработки характеризуется высокими скоростями резания (100-200м/мин) и малыми подачами (0,03-0,1мм/об). Высокие производительность и качество тонкого растачивания получают при использовании резцов с режущей частью из синтетических материалов (кубанит, гексанит),т.к. скорость резания при этом может достигать 600-800м/мин. Расточку проводят на станках для точного растачивания, имеющих одно- и многошпиндельные расточные головки.
В стальных корпусах более производительной отделочной обработка основных отверстий по сравнению с тонким растачиванием является внутреннее шлифование с вращением корпуса в специальных приспособлениях. При диаметре отверстия более 150мм возможно применение планетарного шлифования, когда деталь крепится неподвижно, а шлифовальный круг, вращаясь относительно оси шпинделя, совершает в месте с ним планетарное движение по обрабатываемому отверстию.
При хонингованиии (обработка отверстия поджатыми абразивными брусками) получают высокую точность геометрической формы отверстия и малую высоту микронеровностей обработанной поверхности. Хонингование проводят на одно- и многошпиндельных станках с обильным охлаждением СОЖ, без полного выхода хонголовки из обрабатываемого отверстия. Хонингованием обрабатывают высокоточные отверстия - цилиндры двигателей внутреннего сгорания, отверстия под пиноль задней бабки токарного станка и т.д.
Раскатывание, кроме высокой точности и шероховатости, позволяет получить высокую износостойкость обработанных отверстий за счет пластического деформирования приповерхностных слоев. Проводить этот вид финишной обработки можно на токарных, сверлильных, расточных и других станках.
3. Особенности обработки корпусов на станках с ЧПУ
Наиболее эффективным в условиях мелко- и среднесерийного производства является обработка корпусных деталей на станках с ЧПУ типа «обрабатывающий центр». Благодаря наличию магазина сменных, заранее настроенных на размер инструментов (рис.2.8.), перемещающемуся шпинделю и поворотному столу такой станок может в автоматическом режиме обработать практически все элементы корпуса с четырех сторон, включая фрезерование, сверление, зенкерование, развертывание, нарезание резьбы, растачивание и т.д. с высоким уровнем качества обработки. Следует помнить, что запуску в производство любой корпусной детали предшествует создание управляющей программы для всех механизмов станка. Кроме того, до обработки на станке типа «обрабатывающий центр» на заготовках корпусов необходимо подготовить чистовую технологическую базу.
Рис.2.8. Станок с ЧПУ типа «обрабатывающий центр» с автоматической системой 100 инструментов.
4. Контроль корпусных деталей
У большинства корпусных деталей контролируют: 1)прямолинейность и взаимное расположение основных плоскостей; 2) размеры, форму и взаимное расположение основных отверстий; их межосевые расстояния; 3) расположение осей отверстий относительно основных поверхностей; 4) неперпендикулярность торцевых плоскостей относительно осей отверстий; 5) шероховатость обработки.
Диаметры отверстий проверяют штангенциркулями, нутромерами, предельными калибрами. Взаимное расположение остальных поверхностей корпусных деталей проверяют при помощи контрольных приспособлений, схемы которых изображены на рис.2.9.
Вопросы для самопроверки
- Назовите назначение корпусных деталей.
- Из каких материалов могут изготовляться корпуса?
- Перечислите методы получения заготовок для корпусных деталей.
- Назовите этапы технологического процесса изготовления корпусных деталей и методы их выполнения.
- На каких станках обрабатываются корпуса?
- Каковы по вашему преимущества и недостатки обработки корпусов на станках с ЧПУ?
- Как осуществляется контроль корпусов?
{/spoilers}