Подшипник Исполнитель
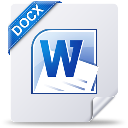
- Скачано: 38
- Размер: 239.5 Kb
Подшипник
Цель занятия: изучить конструкцию подшипников качения скольжения , материалы, и условия работы и виды разрушения, а также рассчитывать их на прочность.
План:
1. Общие сведения и применение
2. Условия работы и виды разрушения
3. Трение и смазка
4.Основные условия образования режима жидкостного трения
5. Практический расчет подшипников скольжения
Расчет подшипников, работающих при полужидкостном трении
Расчет радиальных подшипников жидкостного трения
Пример расчета
6. Краткие сведения о конструкции и материалах подшипников скольжения.
Опорные слова: подшипник, качение, скольжение, применение, условия работы и разрушения, режим трения, критерии расчета, работоспособность, прочность, точность.
{spoiler=Подробнее}
Назначение и классификация
Подшипники служат опорами для валов и вращающихся осей. Они воспринимают радиальные и осевые нагрузки, приложенные к валу, и передают их на раму машины. При этом вал должен фиксироваться в определенном положении и вращаться вокруг заданной геометрической оси. Во избежание снижения к. п. д. механизма потери в подшипниках должны быть минимальными. От качества подшипников в значительной степени зависит работоспособность и долговечность машин.
Подшипники различают по виду трения и по воспринимаемой нагрузке. По первому признаку все подшипники делят на две основные группы:
Подшипники скольжения, у которых опорный участок вала (цапфа — шип, шейка, пята) скользит по поверхности подшипника.
Подшипники качения, у которых трение скольжения заменяют трением качения посредством установки шариков или роликов между опорными поверхностями подшипника и вала.
По второму признаку различают:
1. Радиальные подшипники воспринимающие радиальные нагрузки.
Упорные подшипники воспринимающие осевые нагрузки.
Радиально-упорные подшипники воспринимающие радиальные
и осевые нагрузки.
Все типы подшипников широко распространены.
Подшипники скольжения.
ОБЩИЕ СВЕДЕНИЯ И ПРИМЕНЕНИЕ
Форма рабочей поверхности подшипника скольжения так же, как и форма цапфы вала, может быть цилиндрической (рис. 15.1, а), плоской (рис. 15.1, б), конической (рис. 15.1, е) или шаровой (рис. 15.1, г).
Цапфу, передающую радиальную нагрузку, называют шипом, если она расположена на конце вала, и шейкой при расположении в середине вала. Цапфу, передающую осевую нагрузку, называют пятой, а опору (подшипник) — подпятником.
Подпятники работают обычно в паре с радиальными подшипниками (рис. 15.1, б). Большинство радиальных подшипников (рис. 15.1, а)
Рис.
может воспринимать также и небольшие осевые нагрузки (фиксируют вал в осевом направлении). Для этого вал изготовляют ступенчатым с галтелями, а кромки подшипника закругляют.
Подшипники с конической поверхностью (рис. 15.1, е) применяют редко. Их используют при небольших нагрузках в тех случаях, когда необходимо систематически устранять зазор от износа подшипника.
Рис. 15.2
Также редко применяют и шаровые подшипники. Эти подшипники допускают перекос оси вала, т. е. обладают свойством самоустановки. Пример конструктивного оформления подшипника показан на рис. 15.2. Основным элементом подшипника является вкладыш 1. Вкладыши изготовляют из антифрикционных материалов. Их устанавливают в специальном корпусе подшипника 2 или непосредственно в корпусе машины (станине, раме и т. д.).
Область применения подшипников скольжения в современном машиностроении сократилась в связи с распространением подшипников качения. Однако значение подшипников скольжения в современной технике не уменьшилось. Их применяют очень широко и в целом ряде конструкций они незаменимы. К таким подшипникам относятся:
1. Разъемные подшипники, необходимые по условиям сборки, например, для коленчатых валов.
Высокоскоростные подшипники (>30м/с), в условиях работы
которых долговечность подшипников качения резко сокращается.
Подшипники прецизионных машин, от которых требуется особо
точное направление валов и возможность регулировки зазоров.
Подшипники тяжелых валов (диаметром до 1 м и более), для которых не изготовляют стандартные подшипники качения.
Подшипники, работающие в особых условиях (воде, агрессивных средах и т. п.), в которых подшипники качения неработоспособны.
Подшипники, воспринимающие ударные и вибрационные нагрузки, в которых используется демпфирующее свойство масляного слоя.
Подшипники дешевых тихоходных механизмов и некоторые
другие.
УСЛОВИЯ РАБОТЫ И ВИДЫ РАЗРУШЕНИЯ
Вращению цапфы в подшипнике противодействует момент сил трения. Работа трения нагревает подшипник и цапфу. От поверхности трения тепло отводится через корпус подшипника и вал, а также уносится смазывающей жидкостью. Для любого установившегося режима работы подшипника существует тепловое равновесие: теплоотдача равна тепловыделению. При этом устанавливается определенная температура. Чем больше тепловыделение и хуже условия теплоотдачи, тем выше температура теплового равновесия. Эта температура не должна превышать некоторой предельной величины, допускаемой для данного материала подшипника и сорта смазки. С повышением температуры понижается вязкость масла и увеличивается вероятность заедания цапфы в подшипнике. В конечном результате заедание приводит к выплавлению вкладыша. Перегрев подшипника является основной причиной его разрушения.
Работа подшипника сопровождается износом вкладыша и цапфы, что нарушает правильную работу механизма и самого подшипника. Если износ превышает норму, подшипник бракуют. Интенсивность износа, связанная также с величиной работы трения, определяет долговечность подшипника.
При действии переменных нагрузок (например, в поршневых двигателях) поверхность вкладыша может выкрашиваться вследствие усталости. Усталостное выкрашивание свойственно подшипникам с малым износом и наблюдается сравнительно редко. В случае действия больших кратковременных перегрузок ударного характера вкладыши подшипников могут хрупко разрушаться. Хрупкому разрушению особенно подвержены малопрочные антифрикционные материалы, такие, как баббиты и некоторые пластмассы.
ТРЕНИЕ И СМАЗКА
Режимы трения и критерии расчета
Величина работы трения является основным показателем работоспособности подшипника. Трение определяет износ и нагрев подшипника, а также его к. п. д. Для уменьшения трения подшипники скольжения смазывают.
В зависимости от режима работы подшипника в нем может быть полужи дкостное или жидкостное трение. Схематизированное представление об этих режимах дает рис. 15.3.
При жидкостном трении рабочие поверхности вала и вкладыша разделены слоем масла, толщина h которого больше суммы высот Rz; неров ностей поверхностей
(15.1)
При этом условии масло воспринимает внешнюю нагрузку, предот вращая непосредственное соприкосновение рабочих поверхностей, т.е их износ.
Сопротивление движению в этом случае определяется только внутренним трением в смазочной жидкости. Величина коэффициента жидкостного трения располагается в пределах 0,001 ÷ 0,005 (эта величина может быть меньше коэффициента трения качения).
При полужидкостном трении условие (15.1) не соблюдается, в подшипнике будет смешанное трение — одновременно жидкостное и сухое. Величина коэффициента полужидкостного трения зависит не только от качества масла, но также и от материала трущихся поверхностей. Для распространенных антифрикционных материалов коэффициент полужидкостного трения колеблется от 0,008 до 0,1.
Полужидкостное трение сопровождается износом трущихся поверхностей.
Для работы подшипника самым благоприятным режимом является режим жидкостного трения. Образование режима жидкостного трения является основным критерием расчета подшипников скольжения. При этом одновременно обеспечиваются критерии работоспособности по износу и заеданию.
3.2. Основные условия образования режима жидкостного трения
Исследование режима жидкостного трения в подшипниках основано на гидродинамической теории смазки. Эта теория базируется на решениях дифференциальных уравнений гидродинамики вязкой жидкости, которые связывают давление, скорость и сопротивление вязкому сдвигу. Теоретические решения довольно сложны и поэтому излагаются в специальной литературе (см. [38], [39]). В курсе «Детали машин» изучают принципиальные понятия о режиме жидкостного трения и методику практического расчета подшипников без вывода основных расчетных зависимостей.
На рис. 15.4 показаны две пластины А и Б, залитые маслом и нагружен ные силой Р. Под действием силы Q пластина А движется относительно Б со скоростью υ. Если скорость υ мала (рис. 15.4, а), пластина А выжимает смазку с пластины Б. Поверхности пластин непосредственно соприкасают ся. При этом образуется полужидкостное трение.
При достаточно большой скорости υ (рис. 15.4, б) пластина А поднимает ся в масляном слое и принимает наклонное положение, подобно тому, как поднимается глиссер или водные лыжи, скользящие по воде.
Рис. 15.4
Между пластинами образуется сужающийся зазор. Вязкое и липкое масло непрерывно нагнетается в этот зазор. Протекание масла через сужающийся зазор сопровождается образованием давления р (рис. 15.4, б), которое уравновешивает внешнюю нагрузку. В этом случае движение продолжается в условиях жидкостного трения. Переход к режиму жидкостного трения происходит при некоторой скорости, называемой критической υкр
Гидродинамическая теория смазки доказывает, что гидродинамическое давление может развиваться только в сужающемся зазоре, который принято называть клиновым. В нашем примере начальный клиновый зазор образуется с помощью скошенной кромки пластины А.
Если конструкция подшипника не имеет клинового зазора, в подшипнике не может образоваться жидкостное трение. Например, простой плоский подпятник (см. рис. 15.1, б) не имеет клинового зазора и не может работать при жидкостном трении.
Для образования клинового зазора, а следовательно, и условий жидкостного трения опорной поверхности подпятника придают специальную форму (см. рис. 15.11)..
В радиальных подшипниках клиновая форма зазора свойственна самой конструкции подшипника. Она образуется за счет смещения центров цапфы вала и вкладыша (рис. 15.5, а).
При угловой скорости ω >ωкр. цапфа всплывает в масле и несколько смещается в сторону вращения по траектории, указанной на рис. 15.5, б *. С увеличением угловой скорости увеличивается толщина разделяющего масляного слоя h, а центр цапфы сближается с центром вкладыша. При ω→ расстояние между центрами е → 0 Полного совпадения центров быть не может, так как при этом нарушается клиновая форма зазора, как одно из условий режима жидкостного трения.
Исследования показывают, что для подшипников с определенными геометрическими параметрами толщина масляного слоя h является некоторой функцией характеристики рабочего режима подшипника
Ф
где μω/р — характеристика рабочего режима подшипника; μ — абсолют ная вязкость масла (сопротивление относительному сдвигу слоев
жидкости); ω = πn/30— угловая скорость цапфы; р = Р/ld—условная нагрузка подшипника.
Характер функциональной зависимости (15.2) будет рассмотрен позднее. Здесь отметим только, что толщина масляного слоя возрастает с увеличением вязкости масла и угловой скорости цапфы. С увеличением нагрузки толщина масляного слоя уменьшается.
Таким образом, для образования режима жидкостного трения необходимо соблюдать следующие основные условия:
Между скользящими поверхностями должен быть зазор клиновой формы.
Масло соответствующей вязкости должно непрерывно заполнять
зазор.
Скорость относительного движения поверхностей должна быть
достаточной для того, чтобы в масляном слое создалось давление,
способное уравновесить внешнюю нагрузку.
Известно, что все жидкости и газы обладают вязкостью. Это значит, что при определенных условиях в качестве смазывающей жидкости можно применять воду и даже воздух, что и используется на практике.
ПРАКТИЧЕСКИЙ РАСЧЕТ ПОДШИПНИКОВ СКОЛЬЖЕНИЯ
Расчет подшипников, работающих при полужидкостном трении
К таким подшипникам относятся подшипники грубых тихоходных механизмов, машин с частыми пусками и остановками, неустановившимся режимом нагрузки, плохими условиями подвода смазки и т. п. Эти подшипники рассчитывают:
а) по допускаемому давлению в подшипнике
(15.3)*
б) по допускаемому произведению давления на скорость
(15.4)
где Р — радиальная нагрузка на подшипник; d — диаметр цапфы (вала);l — длина подшипника; — окружная скорость цапфы.
Расчет по [p] предусматривает, в приближенной форме, предупреждение интенсивного износа, перегрева и заедания. Допускаемые значения [р] и [[p] определяют из опыта эксплуатации подобных конструкций
Пример расчета
Радиальный подшипник зубчатой передачи должен работать в режиме жидкостного трения при следующих данных: d = 100 мм, Р = 1000 кгс, и =1000 об/мин; материал вкладыша бронза АЖ9-4.
Решение. 1. Согласно рекомендациям принимаем l/d = 0,8. Находим l = 80 мм; р = Р/ld = 1000/810 = 12.5 кгс/см2 < [р]
2. Предварительно принимаем ψ = 0,001. Находим δ = ψd = 0,1 мм = 100 мкм.
Подбираем посадку , для которой находим (см. справочники или [12]):
δmin= 50 мкм, δmax = 210 мкм, δср = 130 мкм.
Расчет выполняем по δср.=130мкм. и, следовательно,
ψ = δcp/d=0,130/100 = 0,0013 — в рекомендуемых пределах.
3. Назначаем масло -индустриальное 30 и среднюю температуру
t cp =60 0 по графику находим вязкость.μ=0,0014 кгс./м 2
4.Подсчитываем
где ω = πn/30 = π 1000/30 = 105 l/с.
По графику находим χ~0,7.
По формуле h = 130/2 (1 — 0,7) = 19,5 мкм и принимая для цапфы и вкладыша Rz1 = 3,2 мкм и Rz2 = 3,2 мкм, находим
hkp = 1,5 (Rz1 + Rz2) = 1 ,5 (3,2 + 3,2) = 9,6 мкм.
5 Oпределяем запас надежности подшипника
nh = 19,5/9,62 > [nh].
Запас удовлетворительный.
6. Выбираем способ смазки
= = 42,5 < 50— достаточна кольцевая смазка без охлаждения подшипника.
КРАТКИЕ СВЕДЕНИЯ О КОНСТРУКЦИИ И МАТЕРИАЛАХ ПОДШИПНИКОВ СКОЛЬЖЕНИЯ
Конструкция подшипников скольжения весьма разнообразна. Во многом она зависит от конструкции машины, в которой устанавливается подшипник. В настоящей главе рассматриваются только принципиальные конструктивные различия подшипников скольжения.
Очень часто подшипники не имеют специального корпуса. При этом вкладыши размещают непосредственно в станине (рис. 15.8, а) или раме (рис. 15.8, б) машины. Таково например, большинство подшипников двигателей, турбин, станков, редукторов и т. д.
Подшипники с отдельными корпусами (см. рис. 15.2 и рис. 15.9) устанавливают главным образом в таких устройствах, как конвейеры, грузоподъемные машины, трансмиссии и т. д.
В этих случаях подшипники крепят на фермах, стенах, колоннах.
Корпус и вкладыш могут быть неразъемными (см. рис. 15.9) или разъемными (см. рис. 15.2). Разъемный подшипник позволяет легко укладывать вал и ремонтировать подшипник путем повторных расточек вкладыша при его износе. Неразъемные подшипники дешевле. Вкладыши в этих подшипниках обычно запрессовывают в корпус. Разъем вкладыша рекомендуют выполнять перпендикулярно к нагрузке Р или близко к этому положению (рис. 15.10, а). При этом не нарушается непрерывность несущего масляного слоя (см. рис. 15.12).
В тех случаях, когда возможны большие деформации вала или монтаж выполняется неточно, рекомендуется применять самоустанавливающиеся подшипники (рис. 15.10, б). Сферическая поверхность этих подшипников позволяет им поворачиваться в направлении оси вала.
Как отмечалось выше, в подпятниках жидкостного трения необходимо создавать условия для образования клинового зазора. Практиче
Рис. 15.11
ски это достигается, например, выполнением клиновых смазочных канавок в форме сегмента (рис. 15.11, а). Вторым примером подпятника с клиновым зазором является подпятник с качающимися сегментами (рис. 15.11, б). Подпятник имеет несколько сегментов, расположенных по окружности. Опорой сегмента служит сфера, смещенная с оси симметрии сегмента так, чтобы он находился в равновесии при неравномерном давлении масла в зазоре. Когда пята неподвижна, сегмент с ней полностью соприкасается. При вращении пяты под сегмент затягивается масло, и он отклоняется на некоторый угол β, который увеличивается по мере увеличения частоты вращения. Этим достигается автоматическая регулировка клинового зазора, способствующая сохранению режима жидкостного трения.
Смазка подводится в подшипник по ходу вращения цапфы в том месте, где отсутствует гидродинамическое давление р, чаще всего сверху (см. рис. ) или сбоку (см. рис. ). Подвод смазки в зону давления значительно уменьшает несущую способность подшипника. Эпюра давления разорвана в месте подвода смазки, так как давление в подводящем канале всегда мало по сравнению с давлением в зазоре подшипника.
По длине цапфы масло распределяют с помощью смазочных канавок, сообщающихся с подводящим каналом . Смазку подают в подшипник самотеком с помощью специальных устройств (фитильные и капельные масленки, смазочные кольца и т. д.) или под давлением с помощью насосов (плунжерных, шестеренчатых и т. д.).
На практике наблюдаются случаи, когда работа подшипника в режиме жидкостного трения становится неустойчивой и сопровождается вибрацией цапфы. Вибрация свойственна главным образом быстроходным и малонагруженным подшипникам. Одним из признаков возможности образования вибраций является малая величина χ (порядка ≤0,5). Разработано несколько способов устранения вибраций: эллиптическая расточка вкладышей, применение сегментных подшипников, изменение места подвода смазки и т.д.
Для тихоходных тяжелых валов, от которых требуется малое сопротивление вращению, а режим гидродинамического трения обеспечить не удается, применяют гидростатические подшипники. В этих подшипниках несущий масляный слой образуют путем подвода масла под цапфу от насоса под давлением. Давление подбирают таким, чтобы цапфа всплывала в масле.
Гидростатические подшипники используют также для повышения точности центровки валов в прецизионных машинах, для уменьшения износа тяжело нагруженных подшипников в периоды разгона до режима гидродинамической смазки и в некоторых других случаях.
Подшипники с воздушной или газовой смазкой применяют для быстроходных валов (n > 10000 об/мин) при относительно малых нагрузках, а также при работе в условиях высоких температур.
Эти подшипники могут быть аэростатическими и аэродинамическими. В аэростатических подшипниках так же, как и в гидростатических, цапфа поддерживается воздушной подушкой в результате непрерывного поддува сжатого воздуха; в аэродинамических воздушная подушка образуется за счет самозатягивания воздуха в клиновой зазор так же, как и в гидродинамических .
Материал подшипника(основной детали подшипника) должен иметь:
1.Малый коэффициент трения и высокую сопротивляемость заеданию в периоды отсутствия режима жидкостного трения (пуски, торможение и т. п.).
Достаточную износостойкость наряду со способностью к прира
ботке. Износостойкость вкладыша должна быть ниже износостойкости
цапфы, так как замена вала обходится значительно дороже, чем замена
вкладыша.
Достаточно высокие механические характеристики и особенно
высокую сопротивляемость хрупкому разрушению при действии удар
ных нагрузок.
Вкладыши изготовляют из самых разнообразных материалов .
Бронзы оловянистые, свинцовистые, кремнистые, алюминиевые и прочие обладают достаточно высокими механическими характеристиками, но сравнительно плохо прирабатываются и способствуют окислению масла. Бронзы широко применяют в крупносерийном и массовом производствах.
Чугун обладает хорошими антифрикционными свойствами благодаря включениям свободного графита, но прирабатывается хуже, чем бронзы. Его применяют в тихоходных и умеренно нагруженных подшипниках.
Баббит на оловянистой, свинцовистой и других основах является одним из лучших материалов для подшипников скольжения. Он хорошо прира батывается, не окисляет масло, мало изнашивает вал, стоек против заеда ния. Отрицательным свойством баббита является хрупкость и высокая стоимость. Баббитом заливают только рабочую поверхность вкладышей на толщину от 1 до 10 мм. При этом сам вкладыш изготовляют из бронзы, стали, алюминия и т. д.
В целях повышения прочности подшипников, в особенности при переменных и ударных нагрузках, применяют так называемые биметаллические вкладыши, у которых на стальную основу наплавляют тонкий слой антифрикционного материала — бронзы, серебра, сплава алюминия и т. д. Биметаллические подшипники обладают высокой нагрузочной способностью и широко применяются.
Пластмассы на древесной или хлопчатобумажной основе, а также дерево, резина и другие материалы могут работать при водяной смазке. Поэтому их применяют в гидротурбинах и насосах в химическом машиностроении и т. п. Благодаря высокой упругости пластмасс подшипники выдерживают ударные нагрузки и могут компенсировать перекос цапфы.
В последнее время стали применяться и хорошо себя зарекомендовали новые пластмассы типа капрона и др. Тонкий слой этих пластмасс наносят на рабочую поверхность металлического вкладыша. Как показывают исследования, такие вкладыши менее чувствительны к нарушению смазки и выдерживают значительные нагрузки.
Металлокерамические вкладыши изготовляют прессованием при высоких температурах порошков бронзы или железа с добавлением графита, меди, олова или свинца. Большим преимуществом таких вкладышей является высокая пористость. Поры занимают до 20—30% объема вкладыша и используются как маслоподводящие каналы. Металлокерамический подшипник, пропитанный маслом, может в течение длительного времени работать без подвода смазки. Пополнение смазки производится периодической пропиткой или погружением вкладыша в масляный резервуар, образованный в корпусе подшипника. Расход смазки при этом уменьшается до 10 раз.
Вывод: изучив данную тему, студенты изучили конструкцию подшипников, материалы, и условия работы и виды разрушения.
Контрольные вопросы:
1.Для чего служат подшипники?
2.По каким признакам различают подшипники?
3.Какой может быть поверхность подшипника скольжения?
4.Основная причина разрушения подшипника?
{/spoilers}